Quarry By-Products - Material Description
ORIGIN
Processing of crushed stone for use as construction aggregate consists of blasting, primary and secondary crushing, washing, screening, and stockpiling operations.(1) Quarry by-products are produced during crushing and washing operations. There are three types of quarry by-products resulting from these operations: screenings, pond fines, and baghouse fines.Screenings
Screenings is a generic term used to designate the finer fraction of crushed stone that accumulates after primary and secondary crushing and separation on a 4.75 mm (No. 4) sieve. The size distribution, particle shape, and other physical properties can be somewhat different from one quarry location to another, depending on the geological source of the rock quarried, the crushing equipment used, and the method used for coarse aggregate separation. Screenings generally contain freshly fractured faces, have a fairly uniform gradation, and do not usually contain large quantities of plastic fines.(2)
Settling Pond Fines
Pond fines refer to the fines obtained from the washing of a crushed stone aggregate. During production, the coarser size range (greater than No. 30 sieve) from washing may be recovered by means of a sand screw classifier. The remainder of the fines in the overflow are discharged to a series of sequential settling ponds or basins, where they settle by gravity, sometimes with the help of flocculating polymers. Pond clay is a term usually used to describe waste fines derived from the washing of natural sands and gravels.(3)
Baghouse Fines
Some quarries operate as dry plants because of dry climatic conditions or a lack of market for washed aggregate products. Dry plant operation requires the use of dust collection systems, such as cyclones and baghouses, to capture dusts generated during crushing operations. These dusts are referred to as baghouse fines.
It is estimated that at least 159 million metric tons (175 million tons) of quarry by-products are being generated each year, mostly from crushed stone production operations. As much as 3.6 billion metric tons (4 billion tons) of quarry by-products have probably accumulated.(3)
CURRENT MANAGEMENT OPTIONS
RecyclingThe exact quantity of quarry by-products that are being recycled is not known. Very little of the 159 million metric tons (175 million ton) produced annually is thought to be used, especially the pond fines. In a recent survey, three states (Arizona, Illinois, and Missouri) indicated that quarry by-products have been used as an embankment material and three other states (Florida, Georgia, and Vermont) indicated some use of quarry by-products in base or subbase applications.(4) Some use has been made of limestone screenings as agricultural limestone, and baghouse fines from quarry sources have been used as mineral filler in asphalt paving.
Disposal
Virtually all of the quarry by-products generated are disposed of at the quarry source. Screenings are stockpiled in a dry or damp form. Pond fines are conveyed in slurry form to settling ponds. Baghouse fines are usually sluiced into settling ponds.
MARKET SOURCES
Quarry by-products are available at over 3,000 stone quarry operations located in every state except Delaware. Screenings are readily available at most quarries, especially limestone quarries. Although large quantities of pond fines are produced, they must be reclaimed from the ponds and adequately dewatered before they can be considered suitable for use. Baghouse fines are only produced at dry processing plants in areas where there is a lack of market for washed aggregate products. These areas are usually in the more arid regions of the country in the western states.Screenings
At most quarries, screenings are stockpiled separately at or near the primary or secondary crushing equipment. Screenings are essentially a damp, silty, sand-sized material, usually with an estimated 5 to 10 percent moisture content, depending on the length of time the screenings have been stockpiled. The material is easily recovered by using standard excavation equipment and dump vehicles for loading and hauling.
Pond Fines
Pond fines are usually cleaned or removed from settling ponds by draglines, stockpiled for several months to allow for natural dewatering, then truck hauled, usually to another location on the quarry site. Larger production operations may use equipment such as hydrocyclones, clarifiers, thickeners, or belt presses for dewatering the fines. When dredged from settling ponds, the moisture contents of the fines can be as high as 70 to 80 percent. Final moisture contents in the 20 to 30 percent range are attainable, with the degree of dewatering dependent on the mineralogy and gradation of the fines, equipment used, as well as climatic conditions. Unless sufficiently dewatered, pond fines are too wet to be considered a useable material. The physical and chemical properties of settling pond fines can vary widely with aggregate type and source, but are relatively consistent within a single quarry.(3)
Baghouse Fines
The properties of baghouse fines vary with rock type, processing equipment, dust collection equipment, and point of collection within the plant. Baghouse fines, because they are generated as a fine, dry powder, are usually less of a handling problem than either the screenings or the pond fines. For a given aggregate and production source, the physical and chemical properties tend to be relatively uniform over time.(5)
HIGHWAY USES AND PROCESSING REQUIREMENTS
Portland Cement Concrete, Asphalt Concrete, and Flowable Fill AggregateScreenings have properties that are suitable for use as an aggregate substitute in Portland cement concrete, flowable fill, and asphalt paving applications. Baghouse fines and/or pond fines could potentially replace much of the fines in flowable fill mixes, depending on strength requirements, which are usually fairly low.
Granular Base
If properly blended, screenings can potentially be used in granular base courses.
Mineral Filler
Quarry baghouse fines have been successfully used as a mineral filler in asphalt paving. Dewatered pond fines have the potential for use as a mineral filler in hot mix asphalt paving, depending on the clay content of the pond fines.
The only quarry fines by-product that would require significant processing for any of the foregoing applications are the pond fines, which would have to be adequately dewatered before use. Pond fines would require a greater degree of dewatering for use as mineral filler in asphalt than for use in flowable fill.
MATERIAL PROPERTIES
Physical PropertiesScreenings
Screenings are a uniformly sized, fine, sandy material with some silt particles. Screenings commonly range in particle size from 3.2 mm (1/8 in) down to finer than 0.075 mm (No. 200 sieve). Normally, the percentage of particle sizes finer than 0.075 mm (No. 200 sieve) is 10 percent or less by weight. Stockpiles of screenings may contain some particles up to 4.75 mm (No. 4 sieve) in size, which is usually the screen size used for separation. Some weathered rock or overburden material may be present in the screenings from certain processing operations.
Table 1 compares the particle size distribution of the fines fraction (finer than No. 4 sieve) of screenings from several different aggregate sources. Different types of crushers were used to produce these screenings. Despite differences in rock types and crushing machinery, the gradings of the resultant screenings are quite similar.
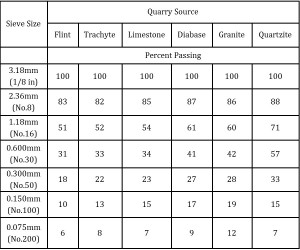
- Pond Fines Pond fines, when initially recovered from the pond, consist of a low solids content, fine-grained slurry, usually with 90 to 95 percent of the particles finer than 0.15 mm (No. 100 sieve) and 80 percent or more of the particles finer than 0.075 mm (No. 200 sieve).Table 2 compares the average particle size distribution of pond fines sampled from two quarries using two different dewatering processes (a sand screw and a U.S. Bureau of Mines dewatering unit). Table 12-2 also includes a listing of gradation ranges for each of the pond fines samples. The table records particle sizing from 0.6 mm (No. 30 sieve) down to the 0.045 mm (No. 325 sieve) size. Within this size range, the grading of the samples is fairly consistent.
- Baghouse Fines Although particle sizing may vary somewhat with fines from different types of stone, the range in particle size is from 0.075 mm (No. 200 sieve) down to 0.001 mm or even finer.Table 3 compares the particle size distribution of 10 different samples of quarry baghouse fines from the processing of four different types of stone. All are predominantly finer than 0.05 mm (No. 270 sieve) and most have a substantial percentage of particles finer than 0.01 mm, although there is some variation in the finer sizes.(5)
There is very little difference in the chemistry or mineralogy of screenings and pond fines from the same quarry or rock source, and also very little difference in the chemistry within the size fractions of the pond fines.(5) Table 4 provides a listing of the chemical and mineralogical constituents of screenings (minus 4.75 mm (No. 4 sieve) material), and pond fines from the same granite quarry. The pond fine components are further subdivided into the overall bulk sample and the portions of the sample that are both coarser and finer than 0.106 mm (No. 140 sieve).
Mechanical Properties
Published data on the mechanical properties (unit weight, compacted density, California Bearing Ratio (CBR), shear strength, etc.) of either screenings, settling pond fines, or baghouse fines are not readily available. The mechanical properties of quarry by-products can be expected to vary according to the type of rock from which the by-products were derived.
Particle Size | Dolomitic Limestone Plant | Diabase Plant | ||||||
Sand Screw | USBM Fines | Sand Screw | USBM Fines | |||||
Average | Range | Average | Range | Average | Range | Average | Range | |
0.600 mm (No. 30 sieve) | 99.9 | 99.2 - 100 | 99.9 | 99.9 - 100 | 100 | 99.9 - 100 | 99.9 | 97.2 - 100 |
0.300 mm (No. 50 sieve) | 99.1 | 97.7 - 99.9 |
99.8 |
99.3 - 99.9 | 99.8 | 99.1 - 100 | 99.3 | 90.2 - 100 |
0.15 mm (No. 100 sieve) | 94.9 | 92.6 - 98.1 | 98.3 | 97.2 - 99.6 | 95.1 | 90.3 - 97.9 | 94.8 | 77.6 - 98.6 |
.075 mm (No. 200 sieve) | 80.4 | 70.8 - 89.1 | 89.9 | 86.4 - 94.6 | 75.2 | 65.0 - 83.6 | 78.3 | 56.8 - 91.8 |
.045 mm (No. 325 sieve) | 61.8 | 47.1-75.9 | 76.1 | 73.0-83.5 | 60.1 | 99.3 - 68.6 | 65 | 42.6 - 81.9 |
Rock Type | Percent Passing Sieve Size | |||||||
.075 mm (No. 200) |
.05 mm (No. 270) | .03 mm | .02 mm | .01 mm | .005 mm | .003 mm | .001 mm | |
Limestone Granite Granite Granite Granite Trap Rock Limestone Limestone Limestone Quartz | 100 100 100 100 100 100 100 100 100 100 | 96 98 89 94 100 98 96 95 95 100 | 82 95 43 69 99 89 93 66 80 100 | 67 84 18 51 96 76 89 37 62 100 | 43 53 8 32 78 48 74 11 43 99 | 23 29 3 16 49 24 46 7 27 93 | 14 17 2 10 32 14 31 5 18 75 | 4 7 1 4 12 5 12 3 7 10 |
Chemical Composition | ||||
Constituent | Screenings | Pond Fines | ||
Bulk | Plus .106 mm (No. 140 sieve) | Minus .106 mm (No. 140 sieve) | ||
SiO2 | 75.25 | 74.98 | 77.44 | 73.37 |
Al2O3 | 13.63 | 13.31 | 12.43 | 14.16 |
K2O | 5.34 | 5.01 | 4.57 | 5.30 |
Na2O | 3.00 | 2.81 | 2.49 | 3.02 |
CaO | 1.28 | 2.07 | 1.00 | 2.77 |
Fe2O3 | 1.22 | 1.28 | 1.28 | 1.27 |
MgO | 0.33 | 0.44 | 0.40 | 0.47 |
MnO | 0.07 | 0.03 | 0.03 | .04 |
Mineralogic Identity | ||||
Constituent | Screenings | Pond Fines | ||
Bulk | Plus .106 mm (No. 140 sieve) | Minus .106 mm (No. 140 sieve) | ||
Quartz | 23.0 | 25.1 | 31.5 | 20.9 |
K-Feldspar | 35.0 | 33.7 | 27.1 | 38.0 |
Plagioclase | 39.2 | 35.7 | 31.1 | 38.7 |
Muscovite | 1.4 | 3.7 | 8.7 | 0.0 |
Biotite | 1.4 | 0.9 | 1.6 | 0.4 |
Diopside | 0.0 | 1.2 | 0.0 | 2.0 |
REFERENCES
- Tepordei, Valentin V. Crushed Stone. U.S. Bureau of Mines Annual Report, Washington, DC, April, 1992.
- Kalcheff, I.V. and C.A. Machemehl, Jr. "Utilization of Crushed Stone Screenings in Highway Construction." Presented at the 59th Annual Meeting of the Transportation Research Board, Washington, DC, January, 1980.
- Wood, Sandra A. and Charles R. Marek. "Recovery and Utilization of Quarry By-Products For Use in Highway Construction." Proceedings of the Symposium on Recovery and Effective Reuse of Discarded Materials and By-Products for Construction of Highway Facilities, Federal Highway Administration, Denver, Colorado, October, 1993.
- Collins, Robert J. and Stanley K. Ciesielski. Recycling and Use of Waste Materials and By-Products in Highway Construction. National Cooperative Highway Research Program Synthesis of Highway Practice No. 199, Transportation Research Board, Washington, DC, 1994.
- Marek, C.R. "Realistic Specifications for Manufactured Sand." Proceedings of the Materials Engineering Congress, Materials Performance and Prevention of Deficiencies and Failures (T. D. White, Editor), Atlanta, Georgia, August, 1992.
Quarry By-Products - Flowable Fill
INTRODUCTION
Quarry by-products (screenings, pond fines, or baghouse fines) can be used as a filler aggregate or as a partial, or possibly a complete, replacement for the pozzolan component in flowable fill mixes. Screenings can be substituted for sand (or other granular filler materials) and may comprise up to as high as 85 percent by dry weight of such mixes. Pond fines or baghouse fines may be used for some, or possibly even all, of the aggregate content and may comprise up to as high as 95 percent by dry weight of flowable fill mixes.(1)PERFORMANCE RECORD
There are no known commercial applications to date that have made use of quarry by-products in flowable fill applications. However, a report prepared for the National Stone Association identifies flowable fill as a promising application for quarry by-products.(2) Most flowable fill applications are designed for comparatively low in-place compressive strength development (from 340 to 1400 kPa (50 to 200 lb/in2)). The use of quarry by-products (screenings, pond fines, or baghouse fines) to replace some or all of the sand filler or fines is not considered detrimental to the strength development of the flowable fill.MATERIAL PROCESSING REQUIREMENTS
ScreeningIt is unlikely that the use of crushed stone screenings as a filler in flowable fill mixes would require any processing since the screenings are produced dry or slightly moist and are generally stockpiled in the same manner as crushed stone or sand and gravel. Minimal sizing on a vibratory screen may be needed if there are any oversize (plus 19 mm (3/4 in)) particles in the screenings. If screenings are stockpiled during a rainy period, some drying may also be necessary.
Dewatering
The use of pond fines as a filler in flowable fill will require some type of dewatering once the fines have been reclaimed from a settling pond. The pond fines may be stockpiled for natural dewatering or passed through a mechanical dewatering device (such as a hydroclone or belt press) to reduce the moisture content.
ENGINEERING PROPERTIES
Some of the engineering properties of quarry by-products that are of particular importance when quarry fines are used in flowable fill mixtures are gradation, moisture content, and unit weight.Gradation: Gradation is important from the perspective of comparing the gradation of commonly used flowable fill materials (such as fly ash and sand) with potential replacement products.
Screenings are nearly all finer than 3.2 mm (1/8 in) and have low percentages (6 to 12 percent) below a 0.075 mm (No. 200 sieve) sieve size. This indicates that screenings are basically well-graded, medium to fine sand-sized materials with a small amount of silt-sized particles.
Recovered pond fines can be expected to have a size range from 100 percent passing 0.59 mm (No. 30 sieve) down to between an average of 75 to 90 percent passing 0.075 mm (No. 200 sieve). This is essentially the same size range as coal fly ash (a common additive in flowable fill mixes), which is a predominantly silt-sized material. Baghouse fines are all finer than 0.075 mm (No. 200 sieve) and nearly all particles are also finer than 0.045 mm (No. 325 sieve). Baghouse fines are nonplastic and similar in sizing and consistency to a finely sized fly ash.
Moisture Content: Screenings, because they are stockpiled in the open, can have a fairly wide range of moisture content within the same stockpile or from one quarry location to another. Pond fines, when reclaimed, may have moisture contents as high as 70 to 80 percent, and must be dewatered, either by stockpiling or by processing. Baghouse fines are available as a dry powder.
Unit Weight: The unit weight of quarry by-products can vary according to the type of rock processed, but is expected to be within the same range as the rock source from which it was derived. Screenings will normally have a higher unit weight than pond fines, with baghouse fines probably being slightly lower in unit weight than pond fines.
Some of the flowable fill mix characteristics of interest include mix strength, flowability, time of hardening, and bleeding and shrinkage.
Mix Strength: Strength development in flowable fill mixes should not be affected to any great extent by the use of quarry by-products. In mixes with high fly ash content, ultimate strengths in excess of 1035 kPa (150 lb/in2) may require jack hammers if removal is necessary.(3) Use of pond fines or baghouse fines in lieu of some of the fly ash should help to maintain the strength development below this value because the pond fines or baghouse fines are not pozzolanic.
On the other hand, if additional strength is required, screenings used in place of all, or a portion of, natural sand should not be detrimental to strength development since quarry screenings are a manufactured sand from the crushing of rock. The particles are mostly angular with good interlocking characteristics and a relatively high angle of internal friction, similar to or possibly even higher than that of natural sand.
Flowability: The use of quarry fines may have an effect on the flowability of a flowable fill mix, depending on the type and amount of quarry fines that are used. The use of pond fines, or baghouse fines, in place of a portion of the mix may cause the mix to be somewhat less flowable at the same moisture content, because of the angularity of the particles of quarry by-products compared with the spherical shape of fly ash particles. Somewhat lower flowability may also occur when using screenings instead of natural sand. To maintain or improve flowability, additional water and/or other additives (such as coal fly ash, which enhances the flowability of the mix) may be needed. Although chemical admixtures (such as water reducing agents) are not ordinarily added to flowable fill mixtures, the use of an appropriate admixture may also help to improve flowability.
Time of Set: Setting time for flowable fill mixes is determined mainly by the cement and water content of the mix, as well as atmospheric conditions. The use of quarry by-products in mixes is not expected to adversely affect the normal setting time of flowable fill mixes in which they are used, provided the cement content of the mix is not altered. Similarly, if pond fines or baghouse fines are used, the time of set should also not be adversely affected as long as the amount of cement in the mix and the water-cement ratio remains essentially the same.
Bleeding and Shrinkage: The use of screenings to replace sand in flowable fill mixes should have minimal effects on bleeding and shrinkage for these mixes. Likewise, the use of pond fines or baghouse fines in lieu of some fly ash in high fly ash content mixes should also not adversely impact bleeding or shrinkage. Evaporation of bleed water in some mixes (e.g., mixes containing high fly ash content) often results in a shrinkage of approximately 10.4 mm per m (1/8 in per ft) of flowable fill depth.(4)
DESIGN CONSIDERATIONS
Mix DesignIn most cases, flowable fill mixes are designed on the basis of a given strength criterion, not on prescribed amounts of ingredients. If quarry by-products are incorporated in these mixes, then specific mix designs will need to be prepared to establish design criteria. The increased fines content in a flowable fill mix when pond fines or baghouse fines are used may require an increase in the water content and/or cement content in order to ensure a flowable mix.(5) With little or no fly ash in the mix, its flowability is likely to be noticeably reduced.
Flowable fill mixtures are usually designed on the basis of compressive strength development, generally after 28 days of ambient temperature curing, but sometimes on the basis of longer term (90 days or more) strength. They are usually designed to have high fluidity (typical slump of 150 mm (6 in) to 200 mm (8 in). In many applications, especially pipe trench backfills where future access for repairs may become necessary, a maximum unconfined compressive strength (usually in the 690 kPa (100 lb/in2) to 1035 kPa (150 lb/in2) range) is the design criteria. For structural support applications, such as abutment backfills supporting bridge approach slabs, the design criteria may range from 4140 kPa (600 lb/in2) to 8280 kPa (1,200 lb/in2).
Screenings
When using screenings to replace all or part of the natural sand in flowable fill mixes, the amount of Portland cement and fly ash used should remain essentially the same. The overall density of the flowable fill mix should not be too different when using screenings, since the screenings have a density that is in the same range as natural sand. Some additional water may be needed, compared with the sand mixes, to achieve a desired range of flowability.
Pond Fines or Baghouse Fines
If pond fines or baghouse fines are to replace part or all of the pozzolan, such as fly ash (in high fly ash content mixes), it is possible that a small increase in the amount of Portland cement in the mix may be needed in order to achieve a desired level of compressive strength. The pond fines or baghouse fines may be somewhat denser than fly ash, resulting in a somewhat increased mix density. Some additional water may also be needed to maintain the desired range of flowability.
Structural Design
Structural design procedures for flowable fill materials are no different than geotechnical design procedures for conventional earth backfill materials. The procedures are based on using the unit weight and shear strength of the flowable fill to calculate the bearing capacity and lateral pressure of the material under given site conditions.
CONSTRUCTION PROCEDURES
Material Handling and StorageThe same general methods and equipment used to handle, store, and stockpile conventional aggregates are applicable for quarry by-products.
Mixing, Placing, and Compacting
Flowable fill can be produced at a central concrete mixing plant in accordance with ASTM C94(6) and delivered by concrete truck mixers or using a mobile, volumetric mixer for small jobs. It is important that high fluidity (slump greater than 150 mm (6 in)) be maintained to ensure that the flowable fill material entirely fills all voids beneath pavements and around structures and utilities.
Quality Control
Various standard field and laboratory tests for flowable fill mixes are given by AASHTO T27,(7) as well as ASTM Provisional Standards 28(8) and 29.(9)
UNRESOLVED ISSUES
Quarry by-products are basically untried in field flowable fill applications. Experience is needed in the design, placement, and performance of flowable fill mixes containing different sources of quarry by-products, including some mixes with coal fly ash. Data are also needed on long-term strength development, flowability, and other engineering properties of such mixes.REFERENCES
- Collins, Robert J. and Samuel S. Tyson. "Utilization of Coal Ash in Flowable Fill Applications." Proceedings of the Symposium on Recovery and Effective Reuse of Discarded Materials and By-Products for Construction of Highway Facilities, Federal Highway Administration, Denver, Colorado, October, 1993.
- Kumar, D.S. and W.R. Hudson. Uses of Quarry Files for Engineering and Environmental Applications. Report for the National Stone Association, Washington, DC, October, 1992.
- Smith, Ann. "Controlled Low-Strength Material." Concrete Construction, May 1991, pp. 389-398.
- Brewer & Associates. An Assemblage of Five Research Reports on the Subject of Controlled Low Strength Material (CLSM). Technical Reports Prepared for the Cincinnati Gas & Electric Company, Cincinnati, Ohio, June, 1992.
- Kumar, D.S. and W.R. Hudson. "Potential Uses for Quarry Fines." Stone Review, Volume 9, No. 2, National Stone Association, Washington, DC, April, 1993, pp. 12-14.
- American Society for Testing and Materials. Standard Specification C94, "Ready-Mixed Concrete," Annual Book of ASTM Standards, Volume 04.02, West Conshohocken, Pennsylvania, 1993.
- American Association of State Highway and Transportation Officials. Standard Method of Test, "Sieve Analysis of Fine and Coarse Aggregates," AASHTO Designation: T27-84, Part II Tests, 14th Edition, 1986.
- ASTM Provisional Standard 28. "Provisional Test Method for Flow Consistency of Controlled Low Strength Materials," American Society for Testing and Materials, West Conshohocken, Pennsylvania.
- ASTM Provisional Standard 29. "Provisional Test Method for Unit Weight, Yield, and Air Content (Gravimetric) of Controlled Low Strength Material," American Society for Testing and Materials, West Conshohocken, Pennsylvania.