Foundry Sand - Material Description
ORIGIN
Foundry sand is a high-quality silica sand that is used to form molds for ferrous (iron and steel) and nonferrous (copper, aluminum, brass, etc.) metal castings. The raw sand is normally of higher quality than typical bank run or natural sands used in construction.(1)The most common casting process used in the foundry industry is the sand cast system. Virtually all sand cast molds for ferrous castings are of the green sand type. Green sand consists of high-quality silica sand, about 5-10 percent bentonite clay (as the binder), 2 to 5 percent water and about 5 percent sea coal (a carbonaceous mold additive to improve casting finish).(2) The term "green sand" is used because molten metal is poured into the mold when the sand is damp or "green".(3) The green sand process constitutes upwards of 90 percent of the molding materials used.(4)
In addition to green sand molds, chemically bonded sand cast systems are also used. These systems involve the use of one or more organic binders (usually proprietary) in conjunction with catalysts and different hardening/setting procedures. Chemical binders include phenolic, furfuryl alcohol, and other inorganic binders.(2) Foundry sand makes up about 97 percent of this mixture. Chemically bonded systems are most often used for "cores" (used to produce cavities that are not practical to produce by normal molding operations) and for molds for nonferrous castings.
Excess foundry sand is typically generated because varying amounts of the previously mentioned additives must continually be reintroduced to the foundry sand to maintain its desired properties, resulting in a larger volume of sand than is needed for the foundry process.(5) In addition, heat and mechanical abrasion eventually render the sand unsuitable for use in casting molds, and a portion of the sand is continuously removed and replaced with virgin sand.(6) The spent sand is either recycled in a non-foundry application or landfilled. Of the 6 to 10 million tons of spent foundry sand generated annually, less than 15 percent is recycled.(6)
Additional information on the production and use of spent foundry sand in construction materials applications can be obtained from:
American Foundrymen's Society, Inc.
505 State Street
Des Plaines, Illinois 60016-8399
http://www.afsinc.org/
Foundry Industry Recycling Starts Today (FIRST)
http://www.foundryrecycling.org
CURRENT MANAGEMENT OPTIONS
RecyclingIn typical foundry processes, sand from collapsed molds or cores can be reclaimed and reused. A simplified diagram depicting the flow of sand in a typical foundry sand molding system is presented in Figure 1. Some new sand and binder is typically added to maintain the quality of the casting and to make up for sand lost during normal operations. (7)
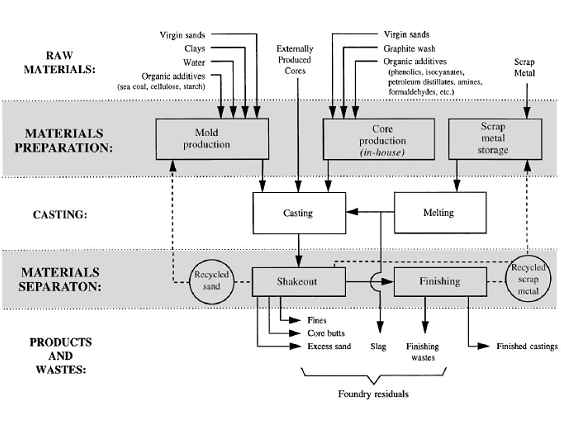
The recycling of spent foundry sand can save energy, reduce the need to mine virgin materials, and may reduce costs for both producers and end users.(6) EPA has found that spent foundry sands produced by iron, steel, and aluminum foundries are rarely hazardous.(6) Despite the support from the EPA, only about 15 percent of spent foundry sands are recycled.(6) This is mainly due to the lack of information on its possible beneficial uses.(9)Beneficial reuse of foundry sand continues to become a more accepted practice as more end-users are introduced to the concept.
As of 2002, eighteen states had programs that regulated beneficial reuse activities for foundry sand,(1) most notably in Wisconsin, Michigan, Illinois, Iowa, Indiana, Minnesota, Pennsylvania, Ohio, California, Texas, and Louisiana.(2) Other countries such as Canada, Spain, Japan, and New Zealand also beneficially use spent foundry sand.(2) Beneficial applications of foundry sand include:
- Aggregate replacement in asphalt mixtures, Portland cement concrete.(6)
- Source material for Portland cement.(6)
- Sand used in masonry mortar mixes.(6)
- Embankments, retaining walls, subbase, flowable fills, barrier layers, and HMA mixtures.(3)
Disposal
Even though many states have developed beneficial reuse regulations for industrial byproducts, large quantities of foundry byproducts are still being landfilled in the United States.(3) However, the scarcity of landfill space as well as an increase in tipping fees and transportation costs has stimulated the pursuit of beneficial reuse of the foundry sand.(10)
State Regulations and Specifications
State regulations of foundry sand reuse are guided by the concept of ensuring the protection of human health and the environment. Rules guiding foundry sand reuse vary from state to state. Some states have a single set of requirements for all industrial by-products, while others have rules specifically guiding the reuse of foundry sand. These rules typically include a requirement for risk assessment for each reuse project and/or developing general concentration thresholds for leachate and contaminants in the waste itself.(11)
Links to regulations guiding the reuse of foundry sand in ten example states including: Illinois, Indiana, Louisiana, Maine, Michigan, New York, Pennsylvania, Texas, West Virginia, and Wisconsin, can be found in the State Toolkit for Developing Beneficial Reuse Programs for Foundry Sand(12) published by the U.S. Environmental Protection Agency. The link to the toolkit is below.
http://www.epa.gov/sustainableindustry/metalcasting/toolkit.pdf
MARKET SOURCES
Currently, there are around 3000 active foundry operations in the United States that generate 6 million to 10 million tons of foundry sand per year.(6)Ferrous industries account for about 95 percent of foundry sand used in metal casting. Spent foundry sand can be obtained directly from foundries, most of which are located in the Great Lakes region.(1) Foundries can also be found in Alabama, California, Louisiana, Tennessee, and Texas.(11)MATERIAL PROPERTIES
Physical PropertiesPhysical properties for spent foundry sand from green sand systems are listed in Table 1.
Table 1. Typical physical properties of spent green foundry sand.
Property | Results | Test Method |
Specific Gravity(1;5;7) | 2.39 - 270 | ASTM D854-06 |
Bulk Relative Density, lb/ft3 (13) | 160.0 | AASHTO T 084 |
Absorption, %(1) | 0.76 - 6.20 | ASTM C128-07a |
Moisture Content, %(1;5;7) | 0.1 - 15.0 | ASTM D2216-05 |
Clay Lumps and Friable Particles(4;7) | 1 - 44 | ASTM C142-97 AASHTO T 112 |
Hydraulic Conductivity (cm/sec)(1;14;15) | 10-3 - 10-9 | ASTM D2434-68 ASTM D5084-03 AASHTO T 215 |
Plastic Index(5;7) | Nonplastic to 12 | ASTM D4318-05 AASHTO T 090 |
The grain size distribution of spent foundry sand is very uniform, with approximately 85 to 95 percent of the material between 0.6 mm and 0.15 mm (No. 30 and No. 100) sieve sizes. Five to 12 percent of foundry sand can be expected to be smaller than 0.075 mm (No. 200 sieve). The particle shape is typically subangular to rounded. Waste foundry sand gradations have been found to be too fine to satisfy some specifications for fine aggregate. A comparison of typical grain size distributions of clean and used foundry sand in comparison with regular concrete sand is illustrated in Figure 2 below.

Spent foundry sand has low absorption, although reported values of absorption were found to vary widely, which can be attributed to the presence of binders and additives.(7) The content of organic impurities (particularly from sea coal binder systems) can vary widely. This may preclude a specific foundry sand from being used in applications where organic impurities are important (e.g., Portland cement concrete aggregate).(17) The specific gravity of foundry sand has been found to vary from 2.39 to 2.70. This variability has been attributed to the variability in fines and additive contents in different samples. (1;7)
In general, foundry sands are dry, with moisture contents less than 2 percent. A large fraction of clay lumps and friable particles have been reported, which are attributed to the lumps associated with the molded sand, which are easily broken up.(7) The variation in hydraulic conductivity, listed in Table 1, is a direct result of the fraction of fines in different foundry sands.
Chemical Properties
Spent foundry sand consists primarily of silica sand, coated with a thin film of burnt carbon and residual binder (bentonite, sea coal, resins, etc.). Table 2 lists the chemical composition of a typical sample of spent foundry sand as determined by x-ray fluorescence.
Constituent | Value (%) |
Silicon dioxide, SiO2 | 85.20 |
Aluminum oxide, Al2O3 | 3.92 |
Iron oxide, Fe2O3 | 3.46 |
Total (SiO2+ Al2O3+ Fe2O3) | 92.58 |
Calcium oxide, CaO | 0.79 |
Magnesium oxide, MgO | 0.58 |
Sodium oxide, Na2O | 0.98 |
Potassium oxide, K2O | 0.17 |
Titanium oxide, TiO2 | 0.21 |
Phosphorus pentoxide, P2O5 | 0.00 |
Manganese dioxide, MnO2 | 0.11 |
Strontium oxide, SrO | 0.01 |
Barium oxide, BaO | 0.07 |
Sulfur trioxide, SO3 | 0.20 |
Loss on ignition, LOI | 5.15 (4) |
Silica sand is hydrophilic and consequently attracts water to its surface. This property could lead to moisture-accelerated damage and associated stripping problems in an asphalt pavement. Antistripping additives may be required to counteract such problems.
Depending on the binder and type of metal being cast, the pH of spent foundry sand can vary from approximately 4 to 8.(13) It has been reported that some spent foundry sands can be corrosive to metals,(19) which can cause the deterioration of metal objects such as underground pipes, culverts, or reinforcing members. The presence of high acidity, pH of 5.5 or less, in soil is also considered a corrosive condition. Soil with a pH of 5.5 or less can react with the lime in concrete to form soluble reaction products that can easily leach out of the concrete. The result is a more porous, weaker concrete.(20)
Few peer-reviewed studies have been conducted to determine organic residues in spent foundry sand or the leachates produced from spent foundry sand. It was found that all spent foundry sands contain polyaronmatic hydrocarbons (PAHs) in which naphthalene is made up about 30 percent of the PAH content.(21) Laboratory studies indicate that organic compounds leach only at low concentrations.(2) With the presence of phenols in chemically bonded foundry sands, there is a possibility that leachate from stockpiles could result in phenol discharges.(13;17;22) Because of the high temperatures encountered during the molding process, residual organic compounds in spent foundry sands are found only in small quantities. Therefore, spent sand, after casting, typically does not contain organic contaminants above regulatory threshold levels, however, fresh casting mixtures and core sand that have not been in contact with hot metal may contain organic contaminants.(2)
Mechanical Properties
Typical mechanical properties of spent foundry sand are listed in Table 3. Spent foundry sand has good durability characteristics as measured by low Micro-Deval abrasion(23) and magnesium sulfate soundness loss tests.(24) The Micro-Deval abrasion test is an attrition/abrasion test where a sample of the fine aggregate is placed in a stainless steel jar with water and steel bearings and rotated at 100 rpm for 15 minutes. The percent loss has been determined to correlate very well with magnesium sulfate soundness and other physical properties. Studies have reported relatively high soundness loss, which is attributed to samples of bound sand loss and not a breakdown of individual sand particles.(7) The internal friction angle of foundry sand has been reported to be in the range of 33 to 40 degrees, which is comparable to that of conventional sands.(7)
Table 3. Typical mechanical properties of spent foundry sand.
Property | Results | Relevant Test Method |
Micro-Deval Abrasion Loss, %(5) | < 2 | ASTM D6928-06 |
Magnesium Sulfate Soundness Loss, % (4;19) | 5 - 15 | ASTM C88-05 |
Internal friction angle (drained)(2;5;7;25) | 33° - 43° | ASTM D4767-04 ASTM D 3080 |
Cohesion intercept (drained), lb/ft2 (2;5;7;25) | 145-585 | ASTM D4767-04 ASTM D 3080 |
Unconfined compressive strength, lb/ft2 (26) | 482-3968 | ASTM D 2166 |
California Bearing Ratio, %(7;26) | 4 - 20 average 20 | ASTM D1883-05 |
Resilient Modulus (MR) regression coefficients(26) | K1 = 122,000 – 248,000 lb/ft2 | AASHTO T-294-94 |
K2 = 0.44 - 0.56 |
DESIGN CONSIDERATIONS
Although specifications for the foundry sand reuse depend largely on the application, general suggestions can be made for improved use of spent foundry sand in roadway applications. An increase in strength in highway subbases using foundry sand can be obtained in the field by compacting the foundry sand-based mixtures using higher compactive efforts. It is recommended that the subbase layer be compacted at dry of optimum for higher strength.(9;26)Compacted foundry sand used as a working platform and subsequently as a contributing subbase member in flexible pavement design has been studied.(27;26;28;29;30) California Bearing Ratio percentages as well as regression coefficients for the power function model to calculate Resilient Modulus, MR, are shown in Table 7-3. Laboratory and case study results show that with proper design and construction, compacted spent foundry sand provides adequate support as a working platform or subbase material.(27;26;28) Design charts for selecting the equivalent thickness of compacted foundry sand for working platforms are provided in reference 29, where a methodology for including the structural contribution of working platforms made from foundry sand or other alternative material is presented in 30.
Lime or cement treatment will have a beneficial effect on the strength of foundry sand mixtures. Addition of lime or cement will increase the unconfined compression and CBR of fully hydrated specimens.(9) Moreover, foundry sand-based subbase specimens have been shown to resist winter conditions better than specimens of reference materials.(9)
ENVIRONMENTAL CONSIDERATIONS
LeachabilityLeachate characterization suggests that foundry sand is generally safe to reuse in highway applications.(31;32;33;34) Spent foundry sand often contains metals and core material containing partially degraded binder. Spent foundry sand may contain leachable contaminants, including heavy metals and phenols that are absorbed by the sand during the molding process and casting operations. Phenols are formed through high-temperature thermal decomposition and rearrangement of organic binders during the metal pouring process.(17)
Spent foundry sand from brass or bronze foundries, in particular, may contain high concentrations of cadmium, lead, copper, nickel, and zinc.(7)However, studies have indicated that foundry sand is less contaminated with metallic elements than foundry dust and slag. Studies also suggest that the constituents in the bulk waste stream of foundry sand exist, but these constituents are not necessarily leachable.(2)
Five widely used standard leaching tests are outlined in Table 4.
Table 4. Extraction Conditions for Different Standard Leaching Tests.(35)
Test Procedure | Method | Purpose | Leaching Medium | Liquid-Solid Ratio | Particle Size | Time of Extraction |
Water Leach Test | ASTM D3987-06 | To provide a rapid means of obtaining an aqueous extract | Deionized water | 20:1 | Particulate or monolith as received | 18 hr |
TCLP | EPA SW-846 Method 1311 | To compare toxicity data with regulatory level. RCRA requirement. | Acetate buffer* | 20:1 | < 9.5 mm | 18 hr |
Extraction Procedure Toxicity (EP Tox) | EPA SW-846 Method 1310 | To evaluate leachate concentrations. RCRA requirement. | 0.04 M acetic acid (pH = 5.0) | 16:1 | < 9.5 mm | 24 hr |
Multiple Extraction Procedure | EPA SW-846 Method 1320 | To evaluate waste leaching under acid condition | Same as EP Toxicity, then at pH = 3.0 | 20:1 | < 9.5 mm | 24 hr extraction per stage |
Synthetic Precipitation Leaching Procedure (SPSL) | EPA Method 1312 | To evaluate metal mobility under actual field conditions, i.e. rain or snow | DI water, pH adjusted to 4.2 to 5 | 20:1 | < 9.5 mm | 18 hr |
* Either an acetate buffered solution with pH = 5 or acetic acid with pH = 3.0 |
A series of leachate tests conducted by the U.S. Department of Energy (DoE) including the TCLP, synthetic precipitation leaching procedure (SPLP), and shake extraction (ASTM D3987) methods indicated that leachates from foundry sand fell within the 95th percentile of metallic element concentrations, below the TCLP thresholds. Their report concluded that foundry sands are generally not hazardous.(36) In an independent study foundry sand specimens evaluated by the EPA Method 1311 and TNRCC Statistic Leaching Test Method showed that contaminants regulated by the EPA were well below regulation limits for hazardous material.(37) A laboratory batch water leach test, column leach test, and below subbase lysimeter study evaluated leachate from gray iron foundry sand. Leachates were analyzed for concentrations of cadmium (Cd), chromium (Cr), selenium (Se), and silver (Ag) and compared to groundwater quality standards for Wisconsin. Peak concentrations in the lysimeters below 84 cm of foundry sand were all above peak concentrations found from the laboratory water leach test and were above the peak concentrations from the laboratory column leach test for both Cr and Se. Peak selenium concentrations in the leachate from the field lysimeters exceeded the Wisconsin groundwater standard. However, with application of dilution factors to account for the reduction in concentration expected between the bottom of the pavement structure and the groundwater table, concentrations would not exceed the groundwater quality standards if the foundry sand layer is at least 1 m above the groundwater table.(38)
The binder system is the primary source of organic contaminants in foundry sand, and green sand systems which generally do not involve organic binders have been shown to have lower potential for leaching organic compounds.(11) The primary organic contaminants from foundry sand are acetone and 1,1,1-trichloroethane.(11) In a DoE sponsored research project, it was found that most organic compounds are burned out during the casting process: 23 of the 37 organic compounds tested were 100 percent below detection limits and 7 were more than 80 percent censored.(36)
Water leach tests on 12 green sands from iron casting foundries showed that leachate test results, when compared to the Wisconsin maximum permissible concentrations, which is the most stringent criteria for reuse of a material that will be placed below the water table, exceeded the limits. However, the concentrations exceeded the maximum permissible concentrations by a small amount and similar concentrations were observed in reactive medium barrier material that is commonly placed below the groundwater table for remediation of contaminant plumes.(39)
Bioassay tests conducted on algae and Dapbnia (representing plant and animal life) included a mixture of pure foundry sand from a foundry in Wisconsin and deionized water produced at a ratio of 1 g of foundry sand for every 4 mL of water. The solution was filtered and the leachate used in the test. The results indicated growth inhibition and showed that in its pure form, foundry sand could be harmful to aquatic life.(40) However, the study concluded that environmental risks markedly decrease or disappear when the foundry sand is mixed with other materials.(40)
Further bioassay tests conducted on 11 foundry sand samples obtained from gray and ductile iron foundries showed that seven out of the 11 foundry sands exhibited bioassay patterns which were equivalent to or better than virgin sand control samples. Four out of the 11 sands exhibited elevated bioassay response levels. The three highest levels of bioassay inhibition were observed in sands from foundries using hot box cores and chemically bound mold binders.(8)
Modeling
Models currently used to simulate leaching from pavement systems and potential impacts to groundwater include STUWMPP,(41) IMPACT,(42)WiscLEACH(43), and IWEM(44). Examples of models in the public domain include WiscLEACH and IWEM. WiscLEACH combines three analytical solutions to the advection–dispersion–reaction equation to assess impacts to groundwater caused by leaching of trace elements from CCPs used in highway subgrade, subbase and base layers. WiscLEACH employs a user friendly interface and readily available input data along with an analytical solution to produce conservative estimates of groundwater impact(43).
The U.S. EPA’s Industrial Waste Management Evaluation Model (IWEM), although developed to evaluate impacts from landfills and stock piles, can help in determining whether leachate will negatively affect groundwater. IWEM inputs include site geology/hydrogeology, initial leachate concentration, metal parameters, and regional climate data. Given a length of time, the program will produce a leachate concentration at a control point (such as a pump or drinking well) that is a known distance from the source. In addition, Monte Carlo simulations can provide worst-case scenarios for situations where a parameter is unknown or unclear. In comparing IWEM to field lysimeter information, it was found that IWEM over predicted the leachate concentrations and could be considered conservative. Overall, however, it was found that IWEM performed satisfactorily in predicting groundwater and solute flow at points downstream from a source.(45) A byproducts module for IWEM will be offered by the EPA in the near future.
An excellent source for detailed information on assessing risk and protecting groundwater is the EPA's "Guide for Industrial Waste Management"(46)which can be found at:
http://www.epa.gov/epaoswer/non-hw/industd/guide/index.asp
According to the EPA, sands from iron, steel, and aluminum manufacturers are, in nearly all cases, non-hazardous. Sands from leaded copper-base facilities, however, may be considered hazardous for toxicity under EPA rules. Due to the general complexity in composition and character of spent foundry sand, appropriate leaching tests should be conducted on foundry sand from a particular source before reuse, although recent studies have suggested that it is not necessary to leachate and measure the full spectrum of metallic elements in the sand.(36)
REFERENCES
A searchable version of the references used in this section is available here. A searchable bibliography of foundry sand literature is available here.- Federal Highway Administration. Foundry sand facts for civil engineers. Federal Highway Administration (FHWA); 2004 May 2004. Report nr FHWA-IF-04-004.
- Winkler E, Bol’shakov AA. Characterization of foundry sand waste. Chelsea Center for Recycling and Economic Development, University of Massachusetts; 2000 Report nr 31.
- Abichou T, Edil TB, Benson CH, Bahia H. Beneficial use of foundry by-products in highway construction. In: Geotechnical engineering for transportation projects: Proceedings of geo-trans 2004, jul 27-31 2004. Los Angeles, CA, United States: American Society of Civil Engineers, Reston, VA 20191-4400, United States; 2004.
- American Foundrymen's Society. Alternative utilization of foundry waste sand, phase I. Des Plaines, Illinois: American Foundrymen's Society Inc.; 1991.
- Goodhue MJ, Edil TB, Benson CH. Interaction of foundry sands with geosynthetics. J Geotech Geoenviron Eng 2001;127(4):353-62.
- Foundry Sands Recycling, EPA530-F-07-018 [Internet]; c2007. Available from: http://www.epa.gov/epaoswer/osw/conserve/foundry/index.asp.
- Javed S, Lovell CW. Use of waste foundry sand in highway construction. Department of Civil Engineering, Purdue University; 1994. Report nr C-36-50N.
- Bastian KC, Alleman JE. Microtox™ characterization of foundry sand residuals. Waste Management 1998 7/1;18(4):227-34.
- Guney Y, Aydilek AH, Demirkan MM. Geoenvironmental behavior of foundry sand amended mixtures for highway subbases. Waste Manage 2006;26(9):932-45.
- Javed S, Lovell CW. Uses of waste foundry sands in civil engineering. Transp Res Rec 1995(1486):109-13.
- EPA, U.S. Environmental Protection Agency (EPA). Beneficial reuse of foundry sand: A review of state practices and regulations. 2002.
- EPA, Environmental Protection Agency. State toolkit for developing beneficial reuse programs for foundry sand. Environmental Protection Agency; 2006.
- Johnson CK. Phenols in foundry waste sand. Modern Casting 1981:273.
- Abichou T, Benson CH. Foundry green sands as hydraulic barriers: Laboratory study. Journal of Geotechnical & Geoenvironmental Engineering 2000 12;126(12):1174.
- Abichou T, Benson CH, Edil TB. Foundry green sands as hydraulic barriers: Field study. J Geotech Geoenviron Eng 2002;128(3):206-15.
- Naik TR, Singh SS. Performance and leaching assessment of flowable slurry. J Environ Eng 2001;127(4):359-68.
- Emery J, Canadian Foundry Association. Spent foundry sand - alternative uses study. Queen’s Printer for Ontario: Ontario Ministry of the Environment and Energy (MOEE); 1993.
- Du L, Folliard K, Trejo D. Effects of constituent materials and quantities on water demand and compressive strength of controlled low-strength material. J Mat in Civ Engrg 2002 November/December 2002;14(6):485-95.
- Emery J. Mineral aggregate conservation - reuse and recycling. Queen’s Printer for Ontario: Ontario Ministry of Natural Resources (MNR); 1992.
- CalTrans. Corrosion guidelines. California Department of Transportation Division of Engineering Services Materials Engineering and Testing Services; 5900 Folsom Blvd., Sacramento, CA 95819, 2003. Report nr Version 1.0.
- Ji S, Wan L, Fan Z. The toxic compounds and leaching characteristics of spent foundry sands. 2001;132(3-4):347-64.
- Ham RK, Boyle WC, Engroff EC, Fero RL. Determining the presence of organic compounds in foundry waste leachates. Modern Casting 1989.
- Ontario Ministry of Transportation. Resistance of fine aggregate to degradation by abrasion in the MicroDuval apparatus. Ontario, Canada: Ontario Ministry of Transportation; 1996. Report nr LS-619.
- AASHTO. Soundness of aggregate by use of sodium sulfate or magnesium sulfate, part II tests. Washington, DC 20001: American Association of State Highway and Transportation Officials; 1999. Report nr T104-99.
- Goodhue M, Edil T, Benson C. Reuse of foundry sands in reinforced earth structures. Madison, WI: Dept. of Civil and Environmental Engineering, University of Wisconsin-Madison; 1998. Environmental Geotechnics Report 98-12.
- Kleven JR, Edil TB, Benson CH. Evaluation of excess foundry system sands for use as subbase material. Transp Res Rec 2000(1714):40-8.
- Kleven JR, Edil TB, Benson CH. Mechanical properties of excess foundry sand for roadway subgrade. Madison, WI: Dept. of Civil and Environmental Engineering, University of Wisconsin-Madison; 1998. Report nr Environmental Geotechnics Report 98-1.
- Edil T, Benson C, Bin-Shafique M, Tanyu B, Kim W, Senol A. Field evaluation of construction alternatives for roadway over soft subgrade. Transp Res Rec 2000;1786:36-48.
- Tanyu BF, Benson CH, Edil TB, Kim W. Equivalency of crushed rock and three industrial by-products used for working platforms during pavement construction. Transp Res Rec 2004(1874):59-69.
- Tanyu BF, Kim W, Edil TB, Benson CH. Development of methodology to include structural contribution of alternative working platforms in pavement structure. Transp Res Rec 2005(1936):70-7.
- Boyle WC, Ham RK. Assessment of leaching potential from foundry process solid wastes. In: Proceedings Purdue Indiana waste conference. Purdue Indiana ed. 1979.
- Ham RK, Boyle WC. Leachability of foundry process solid wastes. Journal of Environmental Engineering 1981 107(1):155-170.
- Ham RK, Boyle WC, Engroff EC, Fero RL. Organic compounds in ferrous foundry process waste leachates. J Envir Engrg 1993;119(1):34-55.
- Ham RK, Boyle WC, Traeger P, Wellender D, Lovejoy M, Hippe JM. Evaluation of foundry wastes for use in highway construction. Wisconsin Departments of Natural Resources and Transportation; Madison, WI: 1993.
- Bin-Shafique S, Benson CH, Edil TB. Geoenvironmental assessment of fly ash stabilized subbases. University of Wisconsin – Madison, Madison, Wisconsin 53706: Geo Engineering Department of Civil and Environmental Engineering; 2002. Geo Engineering Report No. 02-03.
- Tikalsky P, Bahia H, Deng A, Snyder T. Excess foundry sand characterization and experimental investigation in controlled low-strength material and hot-mixing asphalt. U.S. Department of Energy; 2004. Contract No. DE-FC36-01ID13974.
- Wang S, Vipulanandan C. Foundry sand for highway applications. 2000.
- Sauer JJ, Benson CH, Edil TB. Metals leaching from highway test sections constructed with industrial byproducts. Department of Civil and Environmental Engineering, University of Wisconsin-Madison; Madison, Wisconsin 53706: 2005 Geo Engineering Report No. 05-21.
- Lee T, Benson C. Leaching behavior of green sands from gray-iron foundries used for reactive barrier applications. Environmental Engineering Science 2006;23(1):153-67.
- Harrington-Hughes K. Primer environmental impact of construction and repair materials on surface and ground waters. Transportation Research Board, National Research Council, 2101 Constitution Avenue, N.W. Washington, D.C. 20418: National Cooperative Highway Research Program; 2000. Report nr NCHRP Report 443.
- Friend M, Bloom P, Halbach T, Grosenheider K, Johnson M. Screening tool for using waste materials in paving projects (STUWMPP). Office of Research Services, Minnesota Dept. of Transportation, Minnesota; 2004. Report nr MN/RC–2005-03.
- Hesse TE, Quigley MM, Huber WC. User’s guide: IMPACT—A software program for assessing the environmental impact of road construction and repair materials on surface and ground water. NCHRP; 2000. Report nr NCHRP 25-09.
- Li L, Benson CH, Edil TB, Hatipoglu B. Estimating groundwater impacts from coal combustion products in highways. November 2006 2007;159(WR4):151-63.
- EPA, Environmental Protection Agency. Industrial waste management evaluation model (IWEM) User’s guide. Washington, DC: US EPA; 2002. Report nr EPA530-R-02-013.
- Melton JS, Gardner KH, Hall G. Use of EPA’s industrial waste management evaluation model (IWEM) to support beneficial use determinations. U.S. EPA Office of Solid Waste and Emergency Response (OSWER); 2006.
- EPA, Environmental Protection Agency. Guide for Industrial Waste Management [Internet]; c2006. Available from:http://www.epa.gov/epaoswer/non-hw/industd/guide/index.asp.
Foundry Sand - Asphalt Concrete
INTRODUCTION
In the United States, asphalt concrete is used to cover over 2 million miles of roadway, accounting for over 94 percent of all pavements.(1) Foundry sand has been used successfully as a partial replacement for the fine aggregate in hot mix asphalt pavements (HMA).(1;2;3;4) Some general material characteristics must be met when using foundry sand in asphalt concrete pavements. These user guidelines will summarize these characteristics and suggest useful considerations for design and construction of asphalt concrete pavements using spent foundry sand.PERFORMANCE RECORD
Recycled foundry sand has successfully been used in HMA in Pennsylvania, Michigan, and Tennessee.(1) Pennsylvania DOT allows the use of 8 to 10 percent foundry sand in asphalt mixtures.(1) One asphalt producer in Michigan consistently supplies HMA with 10 to 20 percent recycled foundry sand to replace conventional aggregate and meets Michigan DOT specifications.(1) In Tennessee, HMA with 10 percent foundry sand had been reported to compact better and outperform HMA containing washed river sand.(1) Foundry sand has also been used by a hot mix producer in Ontario, Canada since 1994 in both foundation and surface HMA layers.(1)Superpave performance tests in Wisconsin found a potential for positive performance in using recycled foundry sand. In particular, the stability of mixes with recycled foundry sand can be higher than HMA with conventional sand; moisture resistance was higher than mixes with conventional sand; and some mixes demonstrated increased resistance to rutting, while others did not.(5)
MATERIAL PROCESSING REQUIREMENTS
Crushing and ScreeningCrushing and screening of spent foundry sand may be necessary to reduce the size of any oversize core butts or uncollapsed molds prior to use as aggregate. This is readily accomplished using conventional aggregate processing equipment (closed loop crushing and screening process equipped with magnetic separating capabilities). Manufacturing consistency (primarily gradation) is important for HMA production. Variations in sand composition that effect gradation between foundries require that spent foundry sands be examined and evaluated on a source-specific basis.
Quality Control
Sands with fines contents (passing #200) larger than 10 percent may need to be processed to abide by AASHTO M 29. Angularity of the foundry sand can be measured by the fine aggregate angularity test in accordance with AASHTO T 33.(6)
For spent foundry sand to be suitable as a partial replacement for natural fine aggregates in asphalt pavements, it should be free of objectionable materials such as wood, garbage, and metal, which can be introduced at the foundry. Spent foundry sand should also be free of thick coatings of burnt carbon, binders, and mold additives. These constituents can inhibit adhesion of the asphalt cement binder to the foundry sand. Clay clumps can be removed by screening and/or washing, while iron and rubbish can be removed with magnets and/or hand separation.(6)
The clay content and organic-based additives should be quantified and limited when producing an asphalt mix containing spent foundry sand. For many foundry sands, the sand equivalent test (ASTM D2419) is not applicable.(1) Instead, the methylene blue test (AFS 2211-00-S) is a better method for determining the clay content. The loss of ignition test (AASHTO T 267) is a good method for quantifying the fraction of organic-based additives.(1)
Storage and Blending
Stockpiles of sufficient size should be accumulated so that product uniformity can be achieved. This may necessitate the accumulation of a substantial quantity of spent foundry sand in a central site at a specific foundry or group of foundries before transferring the material to hot mix producers.
To satisfy the gradation requirements for HMA fine aggregates (AASHTO M 29),(7) the spent foundry sand must be blended with natural sand at the hot mix plant.
ENGINEERING PROPERTIES
Some of the properties of spent foundry sand that are of particular interest when used in asphalt paving applications include particle shape, gradation, angularity, absorption, clay content, durability, and plasticity. With the exception of gradation, clean, processed foundry sands can generally satisfy the physical requirements for HMA fine aggregate (AASHTO M 29).Particle Distribution: The grain size distribution of spent foundry sand is very uniform, with approximately 85 to 95 percent of the material between 0.6 mm and 0.15 mm (No. 30 and No. 100) sieve sizes.
Gradation: The gradation tends to fall within the limits of a poorly graded fine sand that has relatively uniform size (passing 0.3 mm and retained 0.15 mm), with fines content ranging from 5 to 15 percent. Spent foundry sands have also exhibited a range of P-200 between a minimum of 0.9 percent and a maximum of 16.5 percent.(8) This range is caused by the different amounts of bentonite clay used by foundries.
Angularity: Natural sand has generally been limited to 15 percent by mass of the aggregate blend to minimize round smooth particles that are easier to compact under traffic loads. Recent HMA mixtures have focused on the angularity of fine aggregate. Waste foundry sands have shown a range in angularity between 39.4 and 48 percent which is in the range of low to medium traffic level volumes (minimum 40 percent) to high traffic level volumes (minimum 45 percent).(8) The high angularity of the material appears to be the result of rough surface texture and irregular rounded shapes. The surface texture is the result of burnt additives strongly adhering to the surface.(8)
Absorption: Foundry sand has an absorption between 0.73 and 6.20 percent.(1) In general, a higher percentage of fines contributes to higher absorption percentages which increases both quality and cost.(8)
Durability: Spent foundry sands display good durability characteristics with resistance to weathering.(9)
Plasticity: Spent foundry sand generated by foundries using green sand molding systems, in which bentonite clay and sea coal are added to the casting, should be examined to ensure that plasticity values are below a plasticity index of 4, the maximum allowed by AASHTO M 29. A study of Indiana foundry sand showed that eight out of 10 green sands tested had PI values below 4, yet others have found PIs ranging from non-plastic to as high as 12 percent.(2;10;11) Therefore, the plasticity index of spent foundry sand should be determined before using the sand in an asphalt mix.
Stripping: Stripping is one of the more critical properties that should be assessed when foundry sand is incorporated into an asphalt mix. Spent foundry sand is composed primarily of silica sand, coated with a thin film of burnt carbon, residual binder (bentonite, sea coal, resins), and dust. The hydrophilic nature of the (primarily silica) foundry sand, however, can result in stripping of the asphalt cement coating surrounding the aggregate grains, with resulting loss of fine aggregate and accelerated pavement deterioration. This problem can be mitigated by limiting the content of spent foundry sand in the mix to 15 percent of the total mass of aggregate or using an antistripping additive. Hydrated lime has been used to treat the aggregate against moisture damage.(8)
DESIGN CONSIDERATIONS
Mix DesignAsphalt mixes containing foundry sand can be designed using standard asphalt mix design methods. As expressed previously, the amount of foundry sand used in an asphalt mixture depends largely on the amount of fines in the foundry sand. Studies have shown that foundry sand can be used to replace between 8 and 25 percent of the fine aggregate content in asphalt mixes.(1) Depending on the characteristics of the foundry sand, as much as 19 percent by weight can be used to replace virgin fine aggregates in asphalt mixture. The acceptable amount of foundry sand however can be much lower when the fines content is high or the active clay is higher. It is recommended that foundry sand be considered as another source of aggregates that can be mixed to produce good performance asphalt mixes.(8) HMA pavements with more than the recommended amount of spent foundry sand (blended with natural sand) can be susceptible to moisture damage due to the hydrophilic nature of the (primarily silica) foundry sand, resulting in stripping of the asphalt cement coating surrounding the aggregate grains, loss of fine aggregate, mixture brittleness, and a consequent premature cracking.(2)
The potential for stripping of asphalt mixes containing spent foundry sand should be assessed in the laboratory as part of the overall mix design. Several tests are available, with the most common including: AASHTO T 283(12) which compares the tensile strength ratio of wet and dry specimens; AASTHO T 182,(13) AASHTO T 195,(14) or the Immersion Marshall test following the MTO LS-283(15) procedure, which compares the retained Marshall stability and visual appearance of Marshall briquettes before and after immersion in a heated water bath. The problem of stripping can also be mitigated by adding hydrated lime or commercially available anti-stripping additives.
The optimum asphalt content for HMA mixtures containing various types of foundry sands rages between 5 and 6.2 percent.(8) This is comparable to the asphalt content of mixes not containing foundry sand. As expected, the addition of foundry sand does not significantly change the optimum asphalt content of mixtures.(8;16)
Structural Design
Conventional AASHTO pavement design methods are appropriate for asphalt paving incorporating spent foundry sand as fine aggregate.
CONSTRUCTION PROCEDURES
Material Handling and StorageThe same methods and equipment used for conventional HMA pavement are applicable to pavements containing spent foundry sand. If the foundry sand is dry (less than 5 percent moisture), the sand can be metered directly into a pugmill (batch plants only) or through a recycled asphalt feed (drum plants) where the sand can be further dried, if necessary, by the already heated conventional aggregates.(19)
Foundry sand, which is usually obtained in a dry form, can be stored in covered structures to preserve this condition and reduce energy required for drying. Special measures may be required to control the leachate (containing phenols) from open stockpiles (including temporary stockpiles).(12) The use of an impervious pad (to collect surface moisture or precipitation passing through the stockpile) and subsequent filtration (using an activated carbon filter) of the leachate has proven to be effective (but potentially expensive) in limiting the phenol concentration of the discharge.(6,7)
Mixing, Placing, and Compacting
The same methods and equipment used for conventional hot mix asphalt pavement are applicable to pavements containing spent foundry sand. If it is dry (less than 5 percent moisture), spent foundry sand can be metered directly into a pugmill (batch plants only) or through a recycled asphalt feed (drum plants) where it can be further dried, if necessary, by the already heated conventional aggregates.(13)
The presence of bentonite and organic binder materials can increase the time required for drying and can increase the load on the hot mix plant dust collection system (baghouse). Any coal and organic binders that are present are usually combusted in the process.
The same methods and equipment used for placing and compacting conventional pavements are applicable for pavements incorporating foundry sand.
Quality Control
The same field testing procedures used for conventional HMA mixes should be used for mixes containing foundry sand. Mixes should be sampled in accordance with AASHTO T 168,(20) and tested for specific gravity in accordance with ASTM D2726(21) and in-place density in accordance with ASTM D2950.(22)
PROPOSED USER GUIDELINES
Although recycled foundry sand can be successfully incorporated into asphalt designs, large variability can exist between sands. Each sand be treated as a unique source of aggregate.(16) Furthermore, if the sand contains sodium silicate as a binder, the sand should be rejected. Foundry sand containing bentonite can be washed to reduce the fine content that effects performance.(16)The following steps are suggested for asphalt contractors to introduce foundry sand in HMA mixtures in accordance with the Superpave level 1 (volumetric) design method.(8)
STEP 1: Select gradation and conventional materials that are known to perform well based on past experience.
STEP 2: Obtain a representative sample of the foundry sand and conduct duplicate measures of angularity, absorption, sieve analysis dry and wet, and clay content.
STEP 3: Use an optimization technique to determine optimum amount of sand to be used. The technique should include the gradation of all the materials that are going to be used, including the foundry sand. In addition, constraints for the graduation and the physical properties of fine blend or components should be included. The optimization technique suggested includes gradation limits, cost constraints, minimum angularity requirements, maximum absorption requirements, and maximum clay content requirements.
STEP 4: After obtaining the optimal amounts of foundry sand and aggregates to meet the gradation and the physical property requirements, mix design procedure should be carried out. Select 3 or 4 asphalt contents based on previous tests to mix with the aggregates. Select compaction levels that meet the traffic volume and the local air temperature range following the Superpave volumetric mixture design procedure.
STEP 5: Following the mixing and compaction of the HMA mixtures containing foundry sand, measurements of the samples volumetric properties should be completed. Based on the volumetric results, an optimal asphalt content should be determined to achieve 4 percent air voids. If the volumetric properties failed to meet the Superpave mix design requirements, reexamination of the gradation and the optimization process should be performed. Return to step 1 for selecting new gradation and/or materials.
STEP 6: Hot mix asphalt mixtures at the optimum asphalt content should be mixed and compacted to achieve 7 percent air voids following the AASHTO T 283(12) test procedure. The samples should be examined for moisture susceptibility. If the samples failed, an anti-stripping additive, such as hydrated lime, should be added to the mix, and reexamination should take place.
UNRESOLVED ISSUES
There is a need to establish standard methods of assessing the suitability of spent foundry sand for HMA use. The Immersion Marshall test appears to be appropriate for assessing stripping potential. Also, the influence of spent foundry sand on the moisture susceptibility of HMA should be studied further. The University of Wisconsin-Madison is currently developing better methods to quantify clay and organic-based additives to predict how foundry sands influence moisture damage.(1) There is also a need to further understand the potential for phenol discharges from foundry sand stockpiles, and to determine appropriate treatment strategies, if necessary.REFERENCES
A searchable version of the references used in this section is available here. A searchable bibliography of foundry sand literature is available here.- Federal Highway Administration. Foundry sand facts for civil engineers. Federal Highway Administration (FHWA); 2004 Report nr FHWA-IF-04-004.
- Javed S, Lovell CW, Wood LE. Waste foundry sand in asphalt concrete. Transportation Research Record 1994(1437):27-34.
- Javed S, Lovell CW. Use of waste foundry sand in highway construction. Department of Civil Engineering, Purdue University; 1994 Report nr C-36-50N.
- Collins RJ, Ciesielski SK. Recycling and use of waste materials and by-products in highway construction. Washington, DC: Transportation Research Board; 1994. Report nr National Cooperative Highway Research Program Synthesis of Highway Practice 199.
- Delange K, Braham A, Bahia H, Widjaja M, Romero P, Harman T. Performance testing of hot mix asphalt produced with recycled foundry sand. In: Annual Meeting of the Transportation Research Board; 2001.
- Hughes C. Recycled foundry sand in the mix. Hot Mix Asphalt Technology 2002:29-38.
- AASHTO. Fine aggregate for bituminous paving mixtures, part I specifications. Washington, DC 20001: American Association of State Highway and Transportation Officials; 2003. Report nr M 029-03.
- Miller E, Bahia HU, Benson C, Khatri A, Braham A. Utilization of waste foundry sand in hot mix asphalt mixtures. American Foundry Society Transactions 2001;103(1):1393-407.
- Emery J, Canadian Foundry Association. Spent foundry sand - alternative uses study. Queen’s Printer for Ontario: Ontario Ministry of the Environment and Energy (MOEE); 1993.
- Abichou T, Benson C, Edil T. Beneficial reuse of foundry sands in construction of hydraulic barrier layers. Madison, WI: Dept. of Civil and Environmental Engineering, University of Wisconsin-Madison; 1998. Report nr Environmental Geotechnics Report 98-2.
- Goodhue MJ, Edil TB, Benson CH. Interaction of foundry sands with geosynthetics. J Geotech Geoenviron Eng 2001;127(4):353-62.
- AASHTO. Resistance of compacted bituminous mixtures to moisture induced damage, part II testing. Washington, DC 20001: American Association of State Highway and Transportation Officials; 2003. Report nr T283-03.
- AASHTO. Coating and stripping of bitumen-aggregate mixtures, part II testing. Washington, DC 20001: American Association of State Highway and Transportation Officials; 1986. Report nr T182-84.
- AASHTO. Determining degree of particle coating of bituminous-aggregate mixtures, part II testing. Washington, DC 20001: American Association of State Highway and Transportation Officials; 1986. Report nr T195-67.
- Ontario Ministry of Transportation. Resistance to stripping of asphaltic cement in bituminous mixture by immersion marshall - laboratory testing manual. Ontario Ministry of Transportation; 1995. Report nr LS 283.
- Tikalsky P, Bahia H, Deng A, Snyder T. Excess foundry sand characterization and experimental investigation in controlled low-strength material and hot-mixing asphalt. U.S. Department of Energy; 2004. Report nr Contract No. DE-FC36-01ID13974.
- Johnson CK. Phenols in foundry waste sand. Modern Casting 1981:273.
- Winkler E, Bol’shakov AA. Characterization of foundry sand waste. Chelsea Center for Recycling and Economic Development, University of Massachusetts; 2000 Report nr 31.
- D’Allesandro L, Haas R, Cockfield RW. Feasibility study on the environmental and economical beneficial use of waste foundry sand in the paving industry. University of Waterloo; 1990:Report for MRCO and the Canadian Foundry Group.
- AASHTO. Sampling bituminous paving mixtures, part II tests. Washington, DC 20001: American Association of State Highway and Transportation Officials; 2003. Report nr T168-03.
- ASTM D2726-05a Standard test method for bulk specific gravity and density of non-absorptive compacted bituminous mixtures. In: Annual book of ASTM standards. West Conshohocken, Pennsylvania: ASTM; 2005.
- ASTM D2950-05 Standard test method for density of bituminous concrete in place by nuclear methods. In: Annual book of ASTM standards. West Conshohocken, Pennsylvania: ASTM; 2005.
Foundry Sand - Flowable Fill
INTRODUCTION
Ferrous spent foundry sand can be used as substitute for natural sand (fine aggregate) in flowable fill.(1;2) Natural sand is a major component of most flowable fill mixes. Foundry sand can be used as a replacement for natural fine aggregate because foundry sand consists primarily (greater than 80 percent) of fine uniform silica sand.(3)Flowable fill or controlled low strength material (CLSM) is generally composed of a mixture of sand, fly ash from coal-fired power plants, a small amount of cement, water, and admixtures. Flowable fill is defined by the ACI Committee 229(4) as a cementitious material that is in a flowable (self-leveling) state at the time of placement and that has a specified compressive strength of 1400 kPa (200 lb/in2) or less at 28 days. The unconfined compressive strength (UCS) is typically required to be at least 300 kPa (44 psi). This strength makes it possible for the material to be removed should future excavation be necessary. The applications of flowable fill are numerous and include restoration of utility cuts, backfilling structures, filling abandoned wells, filling voids under existing pavements, and pipe embedments. (See references 5, 6, 7, 2, and 8)
The three key characteristics of flowable fill are strength, flow, and setting time.(3) These characteristics are adjusted by varying the relative proportions of the main constituents of the flowable fill (sand, cement or fly ash, and water). While recycled foundry sand is found to be a suitable substitution for natural sand, the bentonite content can vary widely in foundry sands using clay as a binder, and can lead to variable performance.(3)
The specifications in most jurisdictions for flowable fill materials require that aggregates satisfy ASTM C33.(9) While spent foundry sand may not satisfy the gradation requirements of ASTM C33 for fine aggregates, the uniform, spherical nature of the particles produces a relatively free-flowing mixture.
PERFORMANCE RECORD
Known states that have used spent foundry sand in flowable fill include New York, Pennsylvania, Ohio, Wisconsin, Tennessee, and Indiana.(10;11)Pennsylvania has reported successful use of foundry sand as a sand substitute in flowable fill, as well as Ohio where a field demonstration showed performance on par with conventional sand flowable fills.(10) However, before to 1994, Illinois tried spent foundry sand and considered such use unsuitable due to poor performance and economics.(11)MATERIAL PROCESSING REQUIREMENTS
Crushing and ScreeningCrushing spent foundry sand may be necessary to reduce the size of oversize core butts or uncollapsed molds. The spent foundry sand can also be screened and oversize material from molds and cores that have not completely collapsed should be removed.
Quality Control
For spent foundry sand to be suitable as a replacement for fine aggregate in flowable fill, the sand should be free of objectionable material such as wood, garbage, and metal that can be introduced at the foundry. In addition, the sand should be free of thick coatings of burnt carbon, binders, and mold additives that could inhibit cement hydration.
Storage and Blending
Stockpiles of sufficient size should be accumulated and blended so that a consistent gradation can be achieved before transferring the material to ready-mix concrete plants/flowable fill producers.(12) When aggregates must satisfy the requirements of ASTM C33, the spent foundry sand should be blended with natural or other suitable fine aggregate materials to meet gradation requirements. The presence of organics (from some binder systems such as bentonite clay) may exceed ASTM C33 criteria and therefore should be closely monitored.
ENGINEERING PROPERTIES
Some of the engineering properties of spent foundry sand that are of particular interest when foundry sand is used in flowable fill applications include particle shape, gradation, strength characteristics, soundness, deleterious substances, and corrosivity.Unit Weight: The unit weight of the slurry material is in the range of 1570 to 2115 kg/m3 (98 lb/ft3 to 132 lb/ft3).(13;14)
Particle Shape: The grain size distribution of spent foundry sand is more uniform and somewhat finer than conventional concrete sand.(15) The fineness of spent foundry sand contributes to good suspension, limiting segregation of flowable fill. The spherical shape of spent foundry sand particles contributes to good flow characteristics.
Gradation: Spent foundry sand may not satisfy the ASTM C33 gradation requirement; therefore, it may need to be blended with natural sand or other suitable fine aggregate materials to meet the requirements.
Strength Characteristics: Some organic binder materials can interfere with cement hydration, which produces a low strength development that in most cases is more desirable with flowable fill to permit excavation at a later date. Flowable fill incorporating spent foundry sand aggregates readily satisfies specified limited strength criteria.(3) The addition of fly ash tends to reduce the strength, reduce bleed, and increase setting time of the flowable fill.(16) Bentonite has the effect of reducing the amount of fly ash and increasing the amount of Portland cement necessary to meet strength requirements.(16)
The unconfined compressive strength (UCS) is a function of the water-to-cement ratio as well as the proportion of foundry sand in the mixture.(1;14)Figure 3 shows 7, 28, and 91-day UCS results for varying proportions of foundry sand and fly ash. For low strength mixtures, the UCS is affected by the cement content more strongly than the water-cement ratio (W/C).(17) A large drop in UCS occurs between a W/C of 4 to 6.5, whereas for W/C > 6.5, the UCS is typically in the range of 0.3 to 1.0 MPa (44 lb/in2 to 145 lb/in2).(3)

An empirical relationship was determined between water-cement ratio and 28-day UCS based on two dozen tests using differing types of foundry sand and Class F fly ash: (1)

where Sc is the 28-day unconfined compressive strength in kPa and W/C is the water-cement ratio. Although long-term strength gain can be estimated by the 28-day strength, the increase in 90-day strength is approximately 20 to 30 percent greater than the 28-day strength.(1;3;18)
Flow Behavior: A typical target flow for flowable fill is 230 mm ± 5 mm (9 in ± 0.2 in).(3) Mixtures with foundry sand require considerably more water than mixtures prepared with river sand or base silica.(1) Grain size and bentonite content primarily affect water demand. Finer average grain sizes demand less water, while higher bentonite contents increase water demand.(18) At a bentonite content between 10 and 12 percent, much greater water requirements are necessary as the impedance to flow caused by the bentonite dominates.(3) Fly ash concentration was found to have little affect on flowability apart from a decrease in water demand at low concentrations.(1)
Soundness: The performance of spent foundry sands in soundness tests depends on the amount of clay binder materials present in the spent foundry sand, the amount of agglomeration of the fines, and the coating on the individual particles. The greater amount of clay binder or agglomeration, or the thicker the coatings, the higher the soundness loss. Regardless, spent foundry sands generally exhibit favorable performance in soundness testing, with soundness losses less than 10 percent (indicative of durable aggregate).(15)
Deleterious Substances: Poorly managed spent foundry sand can contain objectionable materials such as wood, garbage, metal, carbon, and dust as well as large chunks of sand. For use in flowable fill, spent foundry sand must be managed to ensure that the sand is clean and processed to the proper sand size. Because both spent foundry sand and fly ash contain porous carbon that uptakes water, to maximize the use of foundry sand, fly ash should be used in lesser amounts, which therefore uses less water and cement.(19) Organic content interferes with hydration of the cement and subsequent strength. The organic content of aggregate can be measured by a color test.(20)
Corrosivity: Depending on the binder and type of metal cast, the pH of spent foundry sand can vary from approximately 4 to 8:(21) therefore, some foundry sand can be corrosive to metals.(22) Others have indicated that flowable fill mixes containing spent foundry sand are noncorrosive because of the absence of chlorides and high pH (11.1 to 12.3).(1)
Lateral Earth Pressures: For retaining wall applications of flowable fill, the coefficient of lateral earth pressure immediately after backfilling can be assumed to be 0.8 - 1.0. The earth pressure decreases very rapidly as the fill gains strength. After 12 hrs, the coefficient of lateral earth pressure can be assumed to be zero.(23)
Hydraulic conductivity: The average hydraulic conductivity of foundry sand flowable fill is between 7.2x10-5 and 2.6x10-6 cm/s.(1;14;13) Lower hydraulic conductivity occurs with higher cementitious content. Higher fly ash mixtures exhibit a decreased permeability likely due to densification of material microstructure from pozzolanic reaction of the fly ash (Table 6).
Table 6. Average permeability of slurry mixes as a function of relative proportions of foundry sand and fly ash.(13)
Foundry Sand (%) | Fly Ash (%) | Hydraulic conductivity (x10-6 cm /s) |
30 | 70 | 4.8 |
50 | 50 | 6.5 |
70 | 30 | 12.6 |
85 | 15 | 64.9 |
DESIGN CONSIDERATIONS
Mix DesignFlowable fill mixes are usually designed on the basis of compressive strength, generally after 28 days of ambient temperature curing, but sometimes on the basis of longer term (90 days or more) strength. Mixes are designed to have high fluidity during placement (typical slump of 150 mm to 200 mm (6 to 8 inches)) and to develop limited strength (typically between 340 kPa and 1400 kPa (50 and 200 lb/in2)), which is sufficient to support traffic without settling, yet can be readily excavated.(24)
Many jurisdictions specify the use of fine aggregates conforming to ASTM C33 in flowable fill, which generally precludes using spent foundry sand unless it is blended with natural sand or other suitable materials.
For bentonite contents greater than 6 percent, no fly ash is necessary because the bentonite will be sufficient to prevent segregation. For bentonite contents less than 6 percent, some fly ash is necessary. The mixes in Table 7 can be used as starting point for mix design.
Table 7. Recommended mix design of flowable fills containing foundry sand.(3)
Mixture Description | Water (kg/m3) | Foundry Sand (kg/m3) | Cement (kg/m3) | Fly Ash (kg/m3) |
No Fly Ash, BC = 6% - 10% | 475 | 1300 | 50 | 0 |
No Fly Ash, BC = 10% - 13% | 500 | 1225 | 45 | 0 |
Fly Ash, BC = 0% - 6% | 475 | 1000 - 1250 | 40 | 150 - 400 |
Structural Design
Structural design procedures for cured flowable fill materials are no different than geotechnical design procedures for conventional earth backfill materials. The procedures are based on using the unit weight and shear strength of the flowable fill to calculate the bearing capacity and lateral pressure of the material under given site conditions.
CONSTRUCTION PROCEDURES
The same methods and equipment used to mix, transport, and place flowable fill made with conventional aggregates may be used for flowable fill incorporating spent foundry sand.Material Handling and Storage
The same general methods and equipment used to handle conventional aggregates are applicable for foundry sand. Laboratory studies indicate that several organic compounds are present in spent foundry sand but leachable only at low concentrations. Studies on green sands have demonstrated lower organic compound leaching potential compared to chemically bonded systems.(25) With the presence of phenols in chemically bonded foundry sands, there is a possibility that leachate from stockpiles could result in phenol discharges.(21;15;26) Because of the high temperatures encountered during the molding process, residual organic compounds in spent foundry sands are found only in small quantities. Therefore, spent sand, after casting, typically does not contain organic contaminants above regulatory threshold levels, however, fresh casting mixtures and core sand that have not been in contact with hot metal may contain organic contaminants.(25)
Mixing, Placing, and Compacting
Flowable fill can be produced at a central concrete mixing plant in accordance with ASTM C94(9) and delivered by concrete truck mixers or using a mobile, volumetric mixer for small jobs. High fluidity (slump greater than 150 mm (6 in)) should be maintained to ensure that the flowable fill material entirely fills all voids beneath pavements and around structures and utilities.
Quality Control
Various standard field and laboratory tests for flowable fill mixes are given by AASHTO T027,(27) ASTM D6103-04 Standard Test Method for Flow Consistency of Controlled Low Strength Material (CLSM),(28) ASTM D6023-02 Standard Test Method for Unit Weight, Yield, Cement Content, and Air Content (Gravimetric) of Controlled Low Strength Material (CLSM).(29)
ENVIRONMENTAL
Leaching of metals from flowable fill is a long process due to the low permeability of the material. Some leaching will occur, however, through diffusion and the permeation of liquid through the mix if the permeability is high enough. The results of a study of leachates from flowable fill mixtures containing foundry sand and Class F fly ash are presented in Table 8. The leachate results of these CLSM materials were below the enforcement standards of the Wisconsin Department of Natural Resources ground-water quality standards and also met practically all the parameters of the drinking water standards.Table 8. Leachate characteristics of fly ash with and without foundry sand.(14)
Parameter | Concentration (mg/L) | Drinking water standards (mg/L) | GWQS | ||||
Enforcement standard (mg/L) | Prevention action limit (mg/L) | ||||||
Foundry Sand (%) | 0 | 50 | 70 | 85 | |||
Iron | <0.01 | <0.01 | <0.01 | <0.01 | - | 0.30 | 0.15 |
Barium | 0.79 | 0.88 | 0.62 | 0.48 | 1.0 | 2.0 | 0.4 |
Magnesium | <0.03 | <0.03 | <0.03 | <0.03 | - | 0.05 | 0.025 |
Zinc | <0.01 | <0.01 | <0.01 | <0.01 | - | 5 | 2.5 |
Arsenic | <0.001 | <0.001 | <0.001 | <0.001 | 0.05 | 0.05 | 0.005 |
Chromium | 0.036 | 0.018 | 0.023 | 0.021 | 0.05 | 0.1 | 0.01 |
Lead | <0.001 | <0.001 | <0.001 | <0.001 | 0.05 | 0.015 | 0.0015 |
Selenium | 0.008 | 0.01 | 0.015 | 0.007 | 0.01 | 0.05 | 0.01 |
Cadmium | <0.0002 | <0.0002 | <0.0002 | <0.0002 | 0.01 | 0.005 | 0.0005 |
Mercury | <0.0002 | <0.0002 | <0.0002 | <0.0002 | - | 0.002 | 0.0002 |
Chloride | <1.0 | <1.0 | 1 | 1 | 250 | 125 |
UNRESOLVED ISSUES
Most existing specifications require that the fine aggregate for flowable fill satisfy ASTM C33. Since foundry sand does not meet the gradation requirements of this standard, there is a need to review gradation requirements and investigate the impact of alternative gradations to permit wider use of spent foundry sand for this application.REFERENCES
A searchable version of the references used in this section is available here. A searchable bibliography of foundry sand literature is available here.- Bhat ST, Lovell CW. Design of flowable fill: Waste foundry sand as a fine aggregate. Transp Res Rec 1996(1546):70-8.
- Ambroise JA, Amoura, Pera J. Development of flowable high volume - fly ash mortars. In: 11th international symposium on the use and management of coal combustion by-products (CCBs). American Coal Ash Association; 1995.
- Dingrando JS, Edil TB, Benson CH. Beneficial reuse of foundry sands in controlled low strength material. Journal of ASTM International 2004;1(6):15-30.
- ACI Committee 229. Controlled low strength materials. Concrete International 1994;16(7):55-64.
- Adaska WS, Krell WC. Bibliography on controlled low-strength materials (CLSM), Concrete International 1992;14(10):42-3.
- Naik TR, Ramme BW, Kolbeck HJ. Filling abandoned underground facilities with CLSM fly ash slurry. Concrete International 1990;12(7):19-25.
- Larsen RL. Sound uses of CLSM in the environment. Concrete International 1990;12(7):26-9.
- Newman FB, Di Gioia AM, Rojas-Gonzalez LF. CLSM backfills for bridge abutments. 11th International Symposium on the use and Management of Coal Combustion by-Products (CCBs) 1995;2.
- ASTM C33-03 standard specification for concrete aggregates. In: Annual book of ASTM standards. West Conshohocken, Pennsylvania: ASTM; 2003.
- Smith E. A review of the literature on the beneficial use of spent foundry sand in flowable fill. The Pennsylvania State University: Dr. Paul J. Tikalsky; 1996.
- Collins RJ, Ciesielski SK. Recycling and use of waste materials and by-products in highway construction. Washington, DC: Transportation Research Board; 1994. Report nr National Cooperative Highway Research Program Synthesis of Highway Practice 199.
- Leidel DS, Novakowski M, Pohlman D, MacRunnels ZD, MacKay MH. External beneficial reuse of spent foundry sand. AFS Transactions 1994;102.
- Naik TR, Singh SS. Permeability of flowable slurry materials containing foundry sand and fly ash. J Geotech and Geoenvir Engrg 1997;123(5):446-452.
- Naik TR, Singh SS. Performance and leaching assessment of flowable slurry. J Environ Eng 2001;127(4):p359.
- Emery J, Canadian Foundry Association. Spent foundry sand - alternative uses study. Queen’s Printer for Ontario: Ontario Ministry of the Environment and Energy (MOEE); 1993.
- Tikalsky P, Gaffney M, Regan R. Properties of controlled low-strength material containing foundry sand. ACI Materials Journal 2000;97(6).
- Abichou T, Edil TB, Benson CH, Bahia H. Beneficial use of foundry by-products in highway construction. In: Geotechnical engineering for transportation projects: Proceedings of geo-trans 2004, jul 27-31 2004. Los Angeles, CA, United States: American Society of Civil Engineers, Reston, VA 20191-4400, United States; 2004. ID: 32; Compilation and indexing terms, Copyright 2006 Elsevier Inc. All rights reserved.
- Tikalsky P, Bahia H, Deng A, Snyder T. Excess foundry sand characterization and experimental investigation in controlled low-strength material and hot-mixing asphalt. U.S. Department of Energy; 2004. Report nr Contract No. DE-FC36-01ID13974.
- Javed S, Lovell CW. Use of waste foundry sand in highway construction. Department of Civil Engineering, Purdue University; 1994 July, 1994. Report nr C-36-50N.
- Federal Highway Administration. Foundry sand facts for civil engineers. Federal Highway Administration (FHWA); 2004 May 2004. Report nr FHWA-IF-04-004.
- Johnson CK. Phenols in foundry waste sand. Modern Casting 1981:273.
- Emery J. Mineral aggregate conservation - reuse and recycling. Queen’s Printer for Ontario: Ontario Ministry of Natural Resources (MNR); 1992 February, 1992.
- Lee K, Cho J, Salgado R, Lee I. Retaining wall model test with waste foundry sand mixture backfill, GTJODJ 2001;24(4):401-408.
- PCA. Cementitious grouts and grouting. Skokie, Illinois: Portland Cement Association; 1990.
- Winkler E, Bol’shakov AA. Characterization of foundry sand waste. Chelsea Center for Recycling and Economic Development, University of Massachusetts; 2000 October 2000. Report nr 31.
- Ham RK, Boyle WC, Engroff EC, Fero RL. Determining the presence of organic compounds in foundry waste leachates. Modern Casting 1989.
- AASHTO. Sieve analysis of fine and coarse aggregates, part II tests. Washington, DC 20001; Washington, DC 20001: American Association of State Highway and Transportation Officials; 2006. Report nr T027-06.
- ASTM D6103-04 standard test method for flow consistency of controlled low strength material (CLSM). In: West Conshohocken, Pennsylvania: ASTM; 2007.
- ASTM D6023-02 standard test method for unit weight, yield, cement content, and air content (gravimetric) of controlled low strength material (CLSM). In: West Conshohocken, Pennsylvania: ASTM; 2007.
Foundry Sand - Portland Cement
Note: The use of foundry sand in Portland cement and Portland cement concrete mixtures is an emerging application area. Published research and case studies on this subject are limited. As such, the use of foundry sand for this application is not well documented, and any use of foundry sand in Portland cement should be considered somewhat experimental. Publication of such uses and laboratory research would aid in the understanding of the performance of foundry sand in Portland cement.INTRODUCTION
Portland cement concrete is a commonly used paving material that consists of approximately 45 percent coarse aggregate, 25 percent fine aggregate, 20 percent cement and 10 percent water.(1) It has been shown that foundry sand can be used in concrete production as a replacement of the fine aggregate portion of the mixture.(1) The following guideline was developed to provide the foundry sand user a comprehensive summary of foundry sand in terms of its physical properties as well as additional design considerations when incorporating foundry sand into Portland cement mixtures.MATERIAL PROPERTIES
Various characteristics of foundry sand can affect the quality of concrete produced. Because foundry sand properties vary depending on the source from which the foundry sand was produced, it is important that adequate testing of the sand is performed. The material characteristics that are most relevant in Portland cement applications include particle size distribution, dust content, density, specific gravity, organic content, and grain shape.(1) These characteristics are described in further detail below.Particle Size Distribution: The fine aggregate particle size distribution of Portland cement is an important characteristic as it can affect concrete workability, porosity, shrinkage and durability. In particular, too many fine particles can lower the concrete strength and adversely affect durability. ASTM C33(2) requires that the fine aggregate used in concrete have a fineness modulus, an index of aggregate fineness, in the range of 2.3 to 3.1.(1) The fineness modulus of foundry sand typically ranges from 0.9 to 1.6.(1) Generally foundry sand is too fine to permit full substitution. The sand has to be blended with a coarser material to meet this specification. In some areas, natural sands lack finer material. Foundry sand can be blended with them as a partial replacement to satisfy the specification.
Dust Content: Dust content is a concern when using foundry sands in Portland cement. A large dust content can interfere with the bonding of cement to the surface of the aggregate and can also increase water demand. As a result, increased dust content reduces the durability of hardened concrete. ASTM C33 allows a maximum of 5% fine aggregate particles to pass the No. 200 sieve.(1)
Density: According to ASTM C330, the density of fine aggregate must be a minimum of 1.20 to 1.76 g/cm3 (75-110 lbs/ft3).(1) A higher density aggregate is required when the concrete will be subjected to high compressive loads.
Specific Gravity: The specific gravity of foundry sand varies from 2.5 to 2.8, depending on the source, which compares very favorably to natural sands.(1) Although specific gravity does not directly relate to concrete quality, it can be used as a quality control indicator.
Organics Content/Deleterious Materials Content: According to ASTM C33, the maximum amount of clay lumps and friable particles allowed is 3%.(1)Organic content is restricted because it interferes with hydration of the cement and its subsequent strength. The organic content of aggregate can be measured by a color test.(1)
Grain Shape: Foundry sand particles are typically angular to rounded.(1) Round particles are desired as they need less water and cement to coat their surface, and they produce a mixture that is more workable. In contrast, angularity increases water demand and cement content to maintain a workable mix.
PROCESSING REQUIREMENTS
Prior to reuse, foundry sand must be processed to ensure optimal performance. In particular, spent foundry sand should be screened and crushed to obtain the desired gradation, and magnetic particles should be separated. These processes will also remove waste and deleterious materials, such as tramp metal and core pieces, preventing technical problems when mixing the cement components.(1)MIX DESIGN
Although there are no specific requirements for mix design of Portland cement using foundry sand, the selection of aggregate used in concrete is of great importance as aggregate properties strongly influence the concrete properties, before and after hardening. Aggregates are classified based on particle size. Fine aggregates consist of sand or crushed stone with particle diameters smaller than 3/8 inch.(1) Coarse aggregates are gravel or crushed stone with particle diameters ranging between 3/8 inch and 2 inches.(1) To achieve optimal performance, aggregate must be:- Clean and free of objectionable materials, including organic material, clay and deleterious contaminants, which can affect bonding of the cement paste to the aggregate
- Strong, hard and durable
- Uniformly graded
ENVIRONMENTAL CONSIDERATIONS
In casting some non-ferrous metals (such as copper, bronze, and brass), lead is often used to decrease the permeability and increase the machineability of the finished casting. As a result, lead concentrations in spent foundry sand from these processes can exceed the EP toxicity criterion for lead set by the U.S. Environmental Protection Agency.(3) Fortunately, applying foundry sand in Portland cement stabilizes the material and can render it non-EP toxic by means of both physical and chemical mechanisms.(3) Cement not only coats the sand particles to physically prevent leaching; cement is also alkaline which causes it to neutralize acids in the mixture which could leach the lead.(3)UNRESOLVED ISSUES
Because spent foundry sand is black, it may cause finished concrete to have a grayish/black tint, which may not be desirable. A 15 percent or less fine aggregate replacement with foundry sand typically produces a minimal color change. In addition, if foundry sand is used in precast manufacturing, the foundry must be able to meet the quantity requirements of the manufacturer.(1)In general, further investigation is needed to determine appropriate mix designs of Portland cement that account for the variability in material properties of foundry sand.
REFERENCES
A searchable version of the references used in this section is available here. A searchable bibliography of foundry sand literature is available here.- Federal Highway Administration. Foundry sand facts for civil engineers. Federal Highway Administration (FHWA); 2004 May 2004. Report nr FHWA-IF-04-004.
- ASTM C33-03 standard specification for concrete aggregates. In: Annual book of ASTM standards. West Conshohocken, Pennsylvania: ASTM; 2003.
- Zirschky J, Piznar M. Cement stabilization of foundry sands. J Envir Engrg 1988;114(3):715-718.
Foundry Sand - Embankment
INTRODUCTION
Although cities surrounding foundries have historically used spent foundry sand as a construction material, past environmental concerns have limited the use of foundry sand in this manner. State DOTs in Wisconsin, Ohio, Iowa, Illinois, and Indiana have characterized the environmental liability associated with spent foundry sand to be the dominant issue limiting its use.(1) A reexamination of the environmental effects of ferrous foundry sand began in the early 1990s. Most of this work showed that foundry sand did not cause groundwater or surface water contamination (see References 2, 3, 4, 5, 6), and that the measured concentrations were below the U.S. EPA drinking water limits.(5) Several states have allowed full use of foundry sand with little or no restrictions, though the majority of states continue to place restrictions on foundry sand use and require some type of encapsulation.(7)Economic and environmental concerns dominate the issue of recycling foundry sand which is creating incentives for foundries to seek states with regulations more favorable to the industry.(8) As a means of reducing the cost of landfilling, foundries are often willing to pass a substantial portion of cost savings to end users of spent sand. For example, savings in material cost for an Indiana Department of Transportation (INDOT) embankment project is estimated to be $145,000 as a result of using spent foundry sand.(9)
PERFORMANCE RECORD
A 275 m long and 9 m high prototype embankment was constructed for the INDOT with 43,000 m3 of spent foundry sand. The highway embankment consisted of three sections constructed of foundry sand, clay, and natural sand. Geotechnical instrumentation of this test section included settlement plates, vertical and horizontal inclinometers, total pressure cells, piezometers, and a sealed double-ring infiltrometer. Environmental monitoring consisted of six groundwater monitoring wells adjacent to the foundry sand and natural sand embankments. Groundwater quality was measured before and after the construction.(1)Prior to construction, a test pad was built to determine method specification for compaction of foundry sand. A smooth drum vibratory roller and a heavy rubber-tire roller were used for comparison. Lifts of 20 cm (8 in) at a water content between 12 and 15 percent compacted using six passes of a rubber-tire roller was found to be optimal. Smooth drum and smooth drum vibratory rollers were found to be relatively ineffective in compacting spent foundry sand.(10)
Geotechnical performance of the foundry sand was found to be comparable to that of the natural sand. Foundry sand had acceptable strength and compressibility with standard penetration N-values ranging from 33 to 54.(11) The hydraulic conductivity of foundry sand can be quite low (<1x10-5cm/s) which is considerably lower than natural sand and cannot be considered free flowing. Leachate collected from a demonstration embankment indicated metal concentrations below regulatory reuse criteria and typically below drinking water standards, indicating that foundry sand would not have a negative impact on environmental quality.(1)
Dust control was found to be an issue during construction. This concern was alleviated by watering the surface regularly.(10) Foreign objects did not pose a serious problem (i.e. punctured tires), although foundry operators should screen out objects at the plant.(10) In all, project managers were pleased with the performance of foundry sand.(1)
ENGINEERING PROPERTIES
The major components of foundry sand are quartz sand (70 to 80 percent), clay (5 to 15 percent), additives (2 to 5 percent), and water (up to 4 percent).(8) Chemical binders include phenolic, furfuryl alcohol, and other inorganic binders.(8) Specific gravity ranges from 2.39 to 2.70.(12;13;14)Grain size distribution is very uniform, with nearly all spent sands containing particles in the range of 0.6 to 0.15 mm.(4) The plasticity index for clay-bound foundry sand can range from nonplastic to 12 percent.(14) The consistency and uniformity of foundry sand may make it a better engineering material than naturally occurring sand.Standard Proctor results on pure foundry sand yield an optimum water content near 12 percent and a maximum dry density near 1750 kg/m3 (109 lb/ft3).(5;14) The addition of 5 percent lime lowers the maximum dry density and increased optimum moisture content whereas the addition of 5 percent cement has little effect on both dry density and water content.(5)
Direct shear tests on loose specimens give a cohesion between 0 and 5 kPa (100 psf) and an internal angle of friction between 30° and 34°.(14)Dense specimens (as-compacted) yield a cohesion between 17 and 28 kPa (334 and 585 lb/ft2) and an internal angle of friction between 39° and 43°.(13;14)
For design with geosynthetics, interaction coefficients from pullout tests ranged from 0.2 and 1.7 in the normal stress range of 10 to 50 kPa (209 to 1044 lb/ft2).(13) Recommendations for design include a frictional efficiency (Eφ = tanδ / tanφ), woven geotextile interaction coefficients (Ci), and geogrid interaction coefficients are shown in Table 5.
Table 5. Recommended parameters for design of foundry sand and geosynthetics.(13)
Parameter | Value |
Frictional efficiency | |
Geotextile | 0.6 |
Geogrid | 0.6 |
Geomembrane (textured) | 0.7 |
Geogrid interaction coefficients | |
Normal stress < 20 kPa (415 lb/ft2) | 1.0 |
Normal stress > 20 kPa (415 lb/ft2) | 0.5 – 0.8 |
Geotextile interaction coefficients | |
Normal stress < 20kPa (415 lb/ft2) | 1.0 |
Normal stress > 20 kPa (415 lb/ft2) | 0.3 – 0.5 |
Hydraulic conductivity of compacted spent foundry sand is generally low and in many cases cannot be considered free flowing. Typical permeability values of compacted foundry sand are in the range of 10-5 to 10-9 cm/s.(1;8;15;16)
Freeze-thaw tests conducted per ASTM D 560(17) show that the resistance of foundry sand to winter conditions was generally better than a reference material (clayey gravel), except for lime amended mixtures which were at the verge of disintegration after eight cycles. The hydraulic conductivity ratio (Kr = Kn/Ki) ranges from 2 to 24 with increasing values for higher cycles. The unconfined compressive ratio (qur = qun/qui) remains nearly constant between the first and eighth cycle after losing 40 to 50 percent of their initial strength after the first cycle.(5)
ENVIRONMENTAL
A study on concentrations of metals in leachate beneath a foundry sand test plot found concentrations comparable to natural soils.(18) Leachates from the waste foundry sand were found to be non-hazardous as defined by the Resource Conservation and Recovery Act and not statistically different from a nearby natural soil embankment.(10) However, studies have found leaching concentrations of zinc, lead, chromium, and iron in foundry sand to be above the U.S. EPA drinking water limits, although the difference was within 10 percent.(19;20)The use of foundry sand as an embankment of fill material is an unencapsulated use and therefore has the potential for contaminant leaching. For leachate testing in embankment applications, the synthetic precipitation leaching procedure (SPLP) is believed to be most representative of fill applications.(21) Use of foundry sand in embankments and as a fill requires good management and care to ensure that no negative impacts occur to the environment. In particular, areas with sandy soils possessing high hydraulic conductivities and areas near shallow groundwater or drinking aquifers should be given careful consideration. An evaluation of groundwater conditions, applicable state test procedures, and water quality standards should be consulted, as well as ensuring proper construction and environmental modeling.
REFERENCES
A searchable version of the references used in this section is available here. A searchable bibliography of foundry sand literature is available here.- Partridge BK, Fox PJ, Alleman JE, Mast DG. Field demonstration of highway embankment construction using waste foundry sand. Transp Res Rec 1999(1670):98-105.
- Ham RK, Boyle WC. Leachability of foundry process solid wastes. Journal of Environmental Engineering 1981;107(1):155-170.
- Lovejoy MA, Ham RK, Traeger PA, Wellander D, Hippe J, Boyle WC. Evaluation of selected foundry wastes for use in highway construction. In: Proceedings of the 1996 19th international Madison waste conference, sep 25-26 1996. Madison, WI, USA: University of Wisconsin-Madison/Extension, Madison, WI, USA; 1996.
- Naik TR, Singh SS. Performance and leaching assessment of flowable slurry. J Environ Eng 2001;127(4):p359.
- Guney Y, Aydilek AH, Demirkan MM. Geoenvironmental behavior of foundry sand amended mixtures for highway subbases. Waste Manage 2006;26(9):932-45.
- Lee T, Benson C. Leaching behavior of green sands from gray-iron foundries used for reactive barrier applications. Environmental Engineering Science 2006;23(1):153-67.
- Abichou T, Edil TB, Benson CH, Bahia H. Beneficial use of foundry by-products in highway construction. In: Geotechnical engineering for transportation projects: Proceedings of geo-trans 2004, jul 27-31 2004. Los Angeles, CA, United States: American Society of Civil Engineers, Reston, VA 20191-4400, United States; 2004.
- Winkler E, Bol’shakov AA. Characterization of foundry sand waste. Chelsea Center for Recycling and Economic Development, University of Massachusetts; 2000. Report nr 31.
- Fox PJ, Mast DG. Geotechnical performance of a highway embankment constructed using waste foundry sand. Purdue Libraries; 1998. Report nr FHWA/IN/JTRP-98/18.
- Fox PJ, Mast DG. Salvaged sand. Civil Engineering 1997;67(11):53.
- Mast DG. Field demonstration of a highway embankment using waste foundry sand. West Lafayette, ID: Purdue University; 1997.
- Federal Highway Administration. Foundry sand facts for civil engineers. Federal Highway Administration (FHWA); 2004 May 2004. Report nr FHWA-IF-04-004.
- Goodhue MJ, Edil TB, Benson CH. Interaction of foundry sands with geosynthetics. J Geotech Geoenviron Eng 2001;127(4):353-62.
- Javed S, Lovell CW. Use of waste foundry sand in highway construction. Department of Civil Engineering, Purdue University; 1994 July, 1994. Report nr C-36-50N.
- Abichou T, Benson CH. Foundry green sands as hydraulic barriers: Laboratory study. Journal of Geotechnical & Geoenvironmental Engineering 2000 12;126(12):1174.
- Abichou T, Benson CH, Edil TB. Foundry green sands as hydraulic barriers: Field study. J Geotech Geoenviron Eng 2002;128(3):206-15.
- ASTM D560-03 standard test methods for freezing and thawing compacted soil-cement mixtures. In: Annual book of ASTM standards. West Conshohocken, Pennsylvania: ASTM; 2003.
- Freber BW. Beneficial reuse of selected foundry waste material. In: Proceedings of the 1996 19th international Madison waste conference. Madison, WI, USA: University of Wisconsin-Madison/Extension, Madison, WI, USA; 1996.
- Lee T, Benson C. Using foundry sands as reactive media in permeable reactive barriers. Madison, WI: Dept. of Civil and Environmental Engineering, University of Wisconsin-Madison; 2002. Report nr Geo Engineering Report 02-01.
- Coz A, Andres A, Soriano S, Irabien A. Environmental behavior of stabilized foundry sludge. J Hazard Mater 2004 2004 Jun 18;109(1-3):95-104.
- Tikalsky P, Bahia H, Deng A, Snyder T. Excess foundry sand characterization and experimental investigation in controlled low-strength material and hot-mixing asphalt. U.S. Department of Energy; 2004. Contract No. DE-FC36-01ID13974.