Recycled Asphalt Shingles - Material Description
ORIGIN
Approximately 11 million tons of asphalt roofing shingle scrap is generated each year in the United States.(3) There are two types of roofing shingle scraps. They are referred to as tear-off roofing shingles, and roofing shingle tabs, also called prompt roofing shingle scrap. Tear-off roofing shingles are generated during the demolition or replacement of existing roofs. Roofing shingle tabs are generated when new asphalt shingles are trimmed during production to the required physical dimensions or from "out-of-spec" shingles. Roofing shingle tab materials that result from shingle manufacture are estimated to range between 5 to 10% of the total production. Manufacturing shingle scraps production is about 1 million tons per year while tear-off shingle waste production is about 10-11 million tons per year so the manufacturing shingle scrap production is the smaller one.Asphalt shingle scrap created during the manufacturing process is generally uniform and homogenous. The content can be certified and free of debris.(3) The quality of tear-off roofing shingles can vary. Tear-off roofing shingles may contain debris such as nails, wood, paper, and plastic that is removed through processing. The aggregate in scrap shingles can be lost in the weathering process that occurs during the service period. As a result, tear-off scrap may contain more than 30% asphalt by weight. The aged binder in tear-off roofing scrap may also be hard or even brittle,(11) but tear-off shingle is easier to shred than factory scrap.
Roofing shingles are produced by impregnating either organic felt produced from cellulose fibers, or glass felt produced from glass fibers, with a hot saturant asphalt, which is subsequently coated on both sides with more asphalt and finally surfaced with mineral granules. Most roofing shingles produced are of the organic felt type. The saturant and coating asphalt need not be the same. Both saturant and coating asphalts are produced by "blowing", a process in which air is bubbled through molten asphalt flux. The heat and oxygen act to change the characteristics of the asphalt. The process is monitored, and the "blowing" is stopped when the desired characteristics have been produced.
The largest component of roofing shingles (60 to 70 percent by mass) is the mineral material. There are several different types in each shingle.(7) They can include ceramic granules (comprising crushed rock particles, typically trap rock, coated with colored, ceramic oxides), lap granules (coal slag ground to roughly the same size as the ceramic granules), backsurfacer sand (washed, natural sand used in small quantities to keep packaged shingles from sticking together), and asphalt stabilizer (powdered limestone that is mixed into the asphalt).
Specifications for roofing shingles are set out in ASTM D255(1) and ASTM D3462.(2) The composition of scrap shingles may vary between different manufactures. Older shingles were likely to be made with more organic material, while new shingles are made with fiberglass mats.(11)
Additional information on recycling of roofing shingle scrap can be obtained from the following organizations:
Construction Materials Recycling Association P.O. Box 122 Eola , IL 60519 www.shinglerecycling.org
CURRENT MANAGEMENT OPTIONS
RecyclingAsphalt shingle scrap is readily recyclable for a variety of reasons which include: 1. it is generated separately or can readily be segregated from other components of the solid waste stream; 2. the processing technology of asphalt shingles needed to meet the requirements for raw material has been successfully refined; and 3. the processed scrap is a valuable raw material in the production of hot mix asphalt (HMA). There are various opportunities to recycle shingles in road construction applications in addition to HMA applications. Some recycling opportunities have proven to be more viable than others. Benefits of recycling asphalt shingles include conservation of landfill space, potentially lower disposal costs for shingle scrap manufactures, reduced cost in the production of HMA and conservation of virgin material.(11) A best management practices manual for recycling asphalt shingles was completed in 2007.(12)
Below is a map showing states with shingle recycling projects and information.
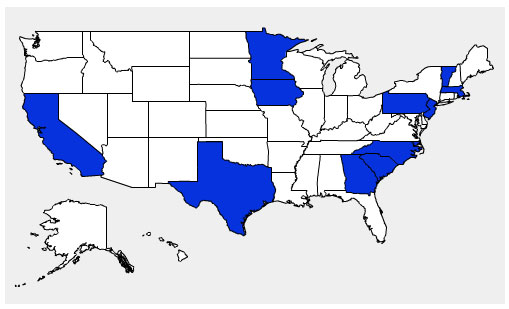
State | Projects/Information |
California | California Integrated Waste Management Board (CIWMB) fact sheets about asphalt shingle recycling:Asphalt Roofing Shingles Recycling: Introduction (CIWMB Pub. #431-97-031 )Asphalt Roofing Shingles in Asphalt Pavement (CIWMB Pub #431-97-033)Asphalt Roofing Shingles in Aggregate Base (CIWMB Pub #431-97-032 )Asphalt Roofing Shingles in Cold Patch (CIWMB Pub #431-98-013 ) |
Georgia | In 1997, the Georgia General Assembly passed legislation encouraging the recycling of asphalt shingles. The legislation also required the Pollution Prevention Assistance Division to work with the Environmental Protection Division to develop a plan to encourage asphalt shingle scrap recycling A report has been prepared in response to this legislative requirement. Asphalt Roofing Shingle Report prepared for the Georgia General Assembly Watson, Donald E., et al., "Georgia's Experience with Recycled Roofing Shingles in Asphaltic Concrete."Georgia Department of Transportation (GDOT), Forest Park, Georgia, 1998. |
Iowa | Iowa Department of Transportation, "Determination and Evaluation for Alternative Methods for Managing and Controlling Highway-Related Dust, Phase II Demonstration Project" with Iowa State University, 2003. Iowa DOT. Iowa Department of Transportation, "Recycled Asphalt Shingles for Slurry Leveling and Crack Filling " with City of Spencer, Iowa, 2002. Iowa DOT .Lohnes, R. A.; Coree, B. J., "Determination and Evaluation of Alternate Methods for Managing and Controlling Highway-Related Dust" , Iowa Department of Transportation, June 30, 2002. Marks, Vernon J., and Petermeier, Gerald, "Let Me Shingle Your Roadway." Research Project HR-2079, Iowa Department of Transportation, Ames, Iowa, 1997. |
Massachusetts | Bauman , Amy, "Asphalt Shingle Recycling in Massachusetts," a study sponsored by The Home Depot Foundation, March 15, 2005. |
Minnesota | Janisch, D. and Turgeon, C., "Minnesota's Experience Using Shingle Scrap in Bituminous Pavements " Report No. MN/PR-96/34, Minnesota Department of Transportation, 1996. NTIS. Krivit, Dan, "An Environmental White Paper Report as Part of the RMRC Project Overcoming the Barriers to Asphalt Shingle Recycling." Prepared for the Minnesota Department of Transportation and the Recycled Materials Resource Center. October 2002. Dan Krivit and Associates . Krivit, Dan, "Driving Change: Solid Waste Management Coordinating Board (SWMCB) Manufacturer Shingle Scrap Recycling Project: Final Report." August 27, 2004. Dan Krivit and Associates. Newcomb, David, et al., "Influence of Roofing Shingles on Asphalt Concrete Mixture Properties." Report MN/RC-93/09, University of Minnesota, Minnesota, 1993. Turgeon, Curtis M., "Waste Tire &Shingle Scrap Bituminous Paving Test Sections On The Munger Recreational Trail Gateway Segment." Office of Materials and Research, Minnesota Department of Transportation, February, 1991. Shingle Recycling Fact Sheets Asphalt Paving Design Guide by Minnesota Asphalt Paving Association (MAPA): Minnesota Mix Specifications, Methods & Quality Control |
New Jersey | Bishop , Gordon, "Jersey firm gets recycling award for use of shingles in road repair"; The Star-Ledger |
North Carolina | Ross , Jr., Ben B., " An Evaluation of the Use of Hot Mix Asphalt Pavements Containing Roofing Shingle Material in North Carolina ." Prepared for the North Carolina Department of Environment, Health and Natural Resources, 1997.NCDOT Asphalt Shingle Slide Show |
Pennsylvania | Boyle , Michael, " Materials-Related Forensic Analysis and Specialized Testing: Laboratory Evaluation of Hot-Mix Asphalt (HMA) Mixtures Containing Recycled or Waste Product Materials Using Performance Testing" , Valley Forge Laboratories Inc., Advanced Asphalt Technologies, LLC, Federal Highway Administration, Pennsylvania Department of Transportation, 2005.Hughes , John J.; Sypolt, Matthew, "Post-Consumer Shingles in HMA" , Pennsylvania Department of Transportation, Federal Highway Administration, Final Report, 2005.Reed , A., " Reclaimed Manufacturer Asphalt Roofing Shingles in Asphalt Mixtures. " Research Project N0. 91-77. Pennsylvania Department of Transportation, 40 pp. 1999. |
South Carolina | Amirkhanian , S N; Vaughan , K M, "Field Evaluation of Use of Waste Shingles in Asphalt Mixtures" , Clemson University , South Carolina Department of Transportation, Federal Highway Administration, 2001. |
Texas | TxDOT Experience with Shingles in HMA - Brochure Button , Joe W., et al., " Roofing Shingles and Toner in Asphalt Pavements. " Research Report 1344-2F, Texas Transportation Institute, College Station , Texas , 1995. (A short summary of the report can be found on the TxDOT site). |
Vermont | Vermont Agency of Natural Resources, " Recycled Shingles in Road Applications ." September 1999. ( Vermont Agency of Natural Resources ) |
Disposal
Most roofing shingle scrap is presently disposed of by landfilling. Approximately shingles represent one third of the waste stream from construction that is landfilled each year.(10) Estimates of the cost for disposing shingles in a landfill may be between $18-$60 per ton.(4)
MARKET SOURCES
Roofing shingle tabs (prompt shingle scrap) can be obtained directly from shingle manufacturers. Tear-off shingle scrap can be obtained directly from roofing contractors or disposal sites that accept the scrap. Information on tab or prompt scrap sources can be obtained from the roofing shingle suppliers or manufacturers.The general composition of asphalt shingles can vary. The typical asphalt shingle components are listed in Table 1.
Component |
Organic Shingles |
Fiberglass Shingles |
Asphalt Cement |
30-35% |
15-20% |
Felt |
5-15% |
5-15% |
Mineral Filler |
10-20% |
15-20% |
Mineral Granules |
30-50% |
30-50% |
The American Society for Testing and Materials (ASTM) has specifications for roofing shingles. The specifications, ASTM D 255-86 (Asphalt Shingles [Organic Felt] Surfaced with Mineral Granules) and ASTM D3462-87 (Asphalt Shingles Made from Glass Felt and Surfaced with Mineral Granules) permit the use of a wide range of products.
Individual shingle manufactures will have more detailed specifications regarding their shingles. Information about the inclusion of asbestos in roofing shingles is inconsistent and therefore it is difficult to quantify its use in roofing shingles. California Integrated Waste Management Board reports that the total asbestos content in asphalt shingles manufactured in 1963 was .02% and in 1977 it had dropped to .00016%. The Georgia department of Transportation however reports that asbestos was used in roofing shingles as late as the 1980s. The Iowa Department of Transportation states that the use of asbestos in roofing shingles was discontinued after 1973. The Iowa Department of Transportation also conducted a study on the asbestos content of roofing shingles. From 368 shingle samples analyzed only 3 contained asbestos, 0.8 %.(9)
HIGHWAY USES AND PROCESSING REQUIREMENTS
Asphalt Cement ModifierTesting has demonstrated that roofing shingle scrap can successfully be incorporated into asphalt mixes. The addition of shingles into hot mix asphalt (HMA) can yield HMA with properties comparable to conventional HMA mixes. Shingles can also be used to create stone matrix asphalt (SMA). Further research needs to be completed in order to reach the optimum SMA mix design. In HMA applications, the asphalt from asphalt shingles will produce in a much stiffer recycled asphalt binder. The use of recycled shingles in HMA will typically result in an improved rutting resistance in the mix. The mix however, may have lower fatigue resistance and a lower low temperature cracking resistance. With the use of a softer virgin binder the fatigue and low temperature performance challenges of the mix can be improved.(4)
Prompt roofing shingle scrap is mainly produced in tabs approximately 285 mm long by 9.5 mm wide by 3 mm thickness (11.5 in by 3/8 in by 1/8 in) which must then be processed to suitable size for introduction into the hot mix asphalt. The asphalt tabs are processed in two stages. The tabs are first shredded using a rotary shredder consisting of two slow-speed blades turning at approximately 50 revolutions per minute. This reduces the chips into smaller, but still quite coarse pieces. The smaller pieces are then reduced to a nominal size of about 9.5 mm (3/8 in) or finer using a high-speed hammermill operating at about 800 to 900 revolutions per minute. To keep the roofing shingle material from agglomerating during processing the material is kept cool by watering at the hammer mill and then stockpiled. The application of water is not very desirable since the processed material becomes quite wet and must be dried prior to introduction into hot mix asphalt.(8) As an alternative to water shreds are sometimes blended with 20% sand or screenings to keep the shingles cool and limit dust. The sand and screenings would otherwise have been added later in the production of HMA and cold mix asphalt patching material; however by adding them earlier in the process it limits the use of water. Recycled asphalt pavement has also been mixed with the shredded shingles in order to prevent stockpile clumping.
Tear-off roofing shingle is easier to shred than factory scrap. The tear-off roofing shingle is hardened with age and as a result it is unlikely it will agglomerate during processing. The debris that contaminates tear-off roofing shingle scrap can be effectively removed. Nails are removed with magnets, paper and other lightweight contaminants are removed with blowers or vacuums.(9)
Roofing Shingles in Cold-Patch Mix Asphalt
Little research has been done in the way of asphalt shingles in cold-applied paving mixes.(9) It may be necessary to heat the mix or add solvents such as diesel, kerosene or asphalt rejuvenating agents to activate the air-blown and possibly aged asphalt in the roofing shingles.(11) The combination of the hard asphalt, uniform and angular aggregate and the entrained cellulose or glass fibers appear to make a quality product that is potentially comparable with other "high performance" cold patch mixes.(9) After the "cold patch" material is placed it is either tapped down with a shovel or driven over. One benefit of a "cold patch" product is that it allows for vehicle traffic to be allowed over the packed area almost immediately after it has been patched.(11)
Aggregate Substitute and Mineral Filler
Roofing shingles incorporated into asphalt paving mixes not only modify the binder, but also, depending on the size of the shredded material, function like aggregate or mineral filler. Organic felt and glass felt particles in particular tend to function like a mineral filler substitute.
Roofing Shingles as Aggregate
The usage of roofing shingles in road applications as an aggregate is becoming much more common, although there is still a need for scientific research. This technology has however been tested in field tests with successful results.(9) Solar heat and the weight from traffic helps to "melt" the shingles into a single mass. This surface could also be used for equipment yards and parking lots.(11)
Roofing Shingles as Aggregate Base Course
Asphalt roofing shingles can be added to a low-end asphalt paving mixture used as an aggregate as an alternative to stones and gravel. This base would support the pavement. Asphalt roofing shingles can be reduced to small pieces about 2.5" or smaller and then added to the mixture. This mixture has the potential to compete effectively with rock and gravel as an alternative ground cover.(11)
Granular Base Stabilization
Ground asphalt shingles may be used as a stabilizer in wet and muddy areas. The asphalt shingles are typically ground and mixed with significant quantities of crushed asphalt pavement for use as ground cover.(11)
MATERIAL PROPERTIES
Roofing shingles are unlike other by-product or secondary materials in that they contain components of fine aggregate, mineral filler, and asphalt cement. There are also differences between the types of shingles (organic and glass felt) produced. As shown in Table 2, organic felt shingles can be expected to exhibit higher moisture content and lower specific gravity than glass felt shingles. Shredded organic felt shingle scrap also exhibits much higher absorption than shredded fiberglass shingle scrap.
Property |
Value |
Maximum Moisture Content Organic Felt Shingles Glass Felt Shingles |
<10% <3% |
Specific Gravity Organic Felt Shingles Glass Felt Shingles |
1.29 1.37 |
Typical physical properties of recovered asphalt cement and the gradation of mineral granules in shingle scrap are listed in Table 3. Asphalt cement in old roofing shingles undergoes oxidative age hardening and stearic hardening (a hardening process in which solid compounds separate from volatile oils in the asphalt cement). Consequently, the asphalt cement in old tear-off roofing shingles is somewhat harder than new asphalt. Although the stearic hardening process has been demonstrated to be reversible by reheating and/or solubilizing,(6) oxidative age hardening is not reversible.
Properties |
New Organic Felt |
New Fiberglass Felt |
Old Roofing Shingles |
Binder Content, % |
Approx. 28% |
Approx. 28% |
30-40% |
Binder Properties: Softening Point, °C (°F) Penetration, dmm (25° C) Ductility, cm (5 cm/min, 25° C) Flash Point, °C (°F) COC |
52-102 (125-215) 23-70 NA >260 (500) |
52-102 (125-215) 23-70 NA >260 (500) |
66-82 (150-180) 20 minimum 25 minimum 232 (450) minimum |
Mineral Material Cumulative Percent Passing 4.75 mm (No.4) 2.36 mm (No.8) 1.0 mm (No.20) 0.3 mm (No.50) 0.15 mm (No.100) |
100 69 45 5 0 |
100 89 65 11 1 |
95-100 55-75 15-35 0-15 0-10 |
ENVIRONMENTAL CONSIDERATIONS
Asbestos content in tear-off roofing shingles continue to be a concern for regulators.(13) A rigorous literature review and compilation of asbestos testing data was compiled in 2007 and found that asbestos was detected in just over 1% of the samples (out of 27,000).(14) Asphalt shingles contain asphalt a petroleum derived product that contains polycyclic aromatic hydrocarbons (PAHs). Questions have been raised as to whether ground up shingles pose a direct or leaching exposure risk, as well as potentially impacting hot mix asphalt plant emissions.(13) There is no literature to indicate emissions at hot mix plants are any different using shingles. Further research on the leachability is currently being conducted in Florida.REFERENCES
- ASTM D255, "Asphalt Shingles (Organic Felt) Surfaced into Mineral Granules." American Society for Testing and Materials, Annual Book of ASTM Standards , Volume 04.04, West Conshohocken , PA , 1996.
- ASTM D3462, "Asphalt Shingles Made From Glass Felt and Surfaced with Mineral Granules." American Society for Testing and Materials,Annual Book of ASTM Standards, Volume 04.04, West Conshohocken , PA , 1996 .
- EPA Region 5: Office of Solid Waste and Emergency Response (OSWER) Factsheet: "OSWER Innovations Pilot: Rear-Off Asphalt Shingles Recycling", May 2005.
- Foo, K.Y., Hanson, D. I., and Lynn, T. A., " Evaluation of Roofing Shingles in Hot Mix Asphalt ," Journal of Materials in Civil Engineering, Vol. 11, No. 1, February 1999, pp 15-20.
- Grodinsky, C., Plunkett, N., Surwilo, J., "Perforrmance of Recycled Asphalt Shingles for Road Applications ", Final Report, Vermont Agency of Natural Resources, Chittenden Solid Waste District, September 2002.
- Grzybowski, K. F. "Recycled Asphalt Roofing Materials - A Multi-Functional, Low Cost Hot-Mix Asphalt Pavement Additive." Use of Waste Materials in Hot-Mix Asphalt, American Society for Testing and Materials Special Technical Publication 1193, American Society for Testing and Materials, Phil adelphia , PA , 1993.
- Newcomb, D., Stroup-Gardiner, M., Weikle, B. and Dresher, A. Influence of Roofing on Asphalt Concrete Mixture Properties . Report prepared for Minnesota Department of Transportation at the University of Minnesota , March, 1993.
- Stroup-Gardiner, M., Newcomb, D. E., and Weikle, B. "Permanent Deformation and Low Temperature Behavior of Roofing Waste Modified HMA", Recovery and Effective Reuse of Discarded Materials and By-Products for Construction of Highway Facilities, Proceedings of FHWA Symposium, Denver, Colorado, October, 1993.
- National Asphalt Pavement Association ( NAPA ) "Special Report 179, Uses of Waste Asphalt Shingles in HMA . January 1997.
- Vermont Agency of Natural Resources, " Recycled Shingles in Road Applications , " September 1999.
- Watson, Donald E., et al., " Georgia's Experience with Recycled Roofing Shingles in Asphaltic Concrete. " TRR 1638, Transportation Research Board. National Research Council, Washington DC 1998.
- Dan Krivit and Associates, " Best Practices Guide", prepared for Construction Materials Recycling Association, October 11, 2007.
- Johnson , J., "Group Tackles Asbestos Concern". Waste News, January 22, 2007
- Townsend, Tim; Powell, Jon; Xu, Chad "Environmental Issues", prepared for Construction Materials Recycling Association Asphalt Shingle Recycling Project, US EPA Innovations Workgroup, Innovative Waste Consulting Services, LLC, October 19, 2007.
Recycled Asphalt Shingles - Asphalt Concrete
INTRODUCTION
In the US about 7-9 million tons of tear off roofing shingles are removed from buildings annually and .05-1 million tons of "out-of-spec" and roofing shingle tabs are generated each year.(26) The cost to dispose of the roofing shingles generated each year ranges between $18 and $60 per ton.(11) Roofing shingle tabs and, with correct processing, tear-off roofing material waste can be used as a replacement for a portion of the asphalt cement and aggregate in hot mix asphalt and as an ingredient in cold mix asphalt patching material. When used in asphalt paving applications, the properties of constituent materials must be well defined and consistent. Because of its consistency and homogeneity, prompt scrap that has been left over from the manufacture of new roofing shingles has been the preferred material for use in asphalt mixtures, but with proper testing and processing, tear-off shingles may also be used. Asphalt shingles also have the potential to be successfully used in a variety of other road construction applications such as an aggregate base course, granular base stabilization medium and an aggregate substitute.(27)PERFORMANCE RECORD
Asphalt Cement ModifierLaboratory studies undertaken during the 1980's suggest that asphalt mixtures containing roofing shingle scrap could exhibit mix design properties similar to that of conventional asphalt mixtures.(23) One of the many advantages to using recycled asphalt shingles in HMA is that the shingles contain ingredients that some HMA manufactures produce to enhance the HMA mixture.(25) Utilization of roofing shingle scrap in hot mix asphalt pavements began in 1990 with trial sections placed in Minnesota.(24) The majority of the research surrounding the reuse of asphalt shingles has focused on potential applications in HMA. Testing or material use has occurred in the following states, Florida, Georgia, Maine, Massachusetts, Missouri, Minnesota, Nevada, New Jersey, New York, Pennsylvania, Maryland, North Carolina, Indiana, Michigan, Tennessee, Texas and Vermont.(13)
The University of Minnesota conducted bench studies on the use of roofing shingles. They concluded: 1. the use of roofing shingles in HMA requires less compaction effort to densify; 2. a mix using 5% of factory scrap shingles resulted in a substantial decrease in cold climate susceptibility; 3. mixtures with more than 5% shingles may have a significant decrease in mixture stiffness without a corresponding positive influence on cold temperature susceptibility. This may result in an unacceptable stress at high temperatures and high traffic volumes; 4. There is no apparent moisture sensitivity by the inclusion of recycled asphalt shingles in HMA; 5. felt-backed shingle mixes have an increased tendency to deform in cold temperatures before thermal cracking occurred. The tear-off and fiberglass-backed shingles both failed to exhibit such behavior; 6. Creep compliance analyses led researches to conclude that deformation was reduced when shingles were added to a mix prepared with a softer (120/150 penetration) asphalt, but that the opposite was true when shingles were added to mixtures using the harder (85/100 penetration) asphalt.(20)
The Minnesota Department of Transportation concluded in their 1996 final report "Minnesota's Experience Using Shingle Scrap in Bituminous Pavements": 1. that the extracted asphalt cement in shingle mixtures is harder than the asphalt cement in control sections of their study(15) which is consistent with laboratory studies;(11) 2. The increase in asphalt cement has not resulted in any added cracking; 3. There will be an economic benefit of using recycled shingles in HMA if the processing and incorporation of shingle scrap is less than the cost for asphalt cement.(15)
The Georgia Department of Transportation paved test sections of highway. They have concluded that the material properties were similar to that of conventional HMA mix. It also appears that the shingle modified mix hardens faster than conventional HMA. Field observations have indicated that the recycled shingle HMA is performing comparably to the control sections paved with conventional HMA. Furthermore Georgia, based on economic estimates, asserts that the incorporation of 5% scrap shingles would reduce the cost of HMA by about $1.70 per ton in Georgia. The disposal cost for shingles in Georgia is about $16.50 per ton, where as process costs were about $5.00 a ton, resulting in an evident economic incentive.(13)
Typical addition rates for roofing shingle scrap in hot mix asphalt have ranged from 3 to 6 percent (by mass). Evaluations of a New Jersey trial pavement section after a few years of service have indicated that performance similar to conventional hot mix asphalt pavements can be expected, with no significant differences in rut depth, cracking, or skid resistance.(3) Roofing shingle scrap has also been used in hot mix asphalt for private sector (commercial/ industrial) work in Florida, Minnesota, and Michigan.(17, 18)
Hazardous waste regulatory leachate test data utilizing the toxicity characteristic leaching procedure (TCLP) indicate that the leachate from processed asphalt roofing shingle scrap is well below hazardous waste EPA limits.(22) However, tear-off roofing shingles may contain significant concentrations of polynuclear aromatic hydrocarbons that are present in roofing tar, and there is some concern that asphalt plant air emissions could be impacted during hot mix asphalt production.(17, 18)
Research of recycled shingles in HMA applications, concludes that the asphalt from asphalt shingles will produce in a much stiffer recycled asphalt binder. The use of recycled shingles in HMA will typically result in an improved rutting resistance in the mix. The mix however, may have lower fatigue resistance and a lower low temperature cracking resistance. With the use of a softer virgin binder the fatigue and low temperature performance challenges of the mix can be improved.(11) Using 5% recycled asphalt shingles in HMA results in a cost savings of between $1.00/ton and $2.00/ton.(25)
Roofing Shingles in Cold-Patch Mix Asphalt
Recycled asphalt shingles have been cited as contributing to improved performance of cold mix asphalt repair materials (pothole repair materials) in Illinois and New Jersey.(4,5) The New Jersey Department of Transportation paved a small section of a low volume traffic ramp with "RePave" a shingle based product marketed as a pothole patching medium. New Jersey was ultimately pleased with the product's performance, however "RePave" is no longer available commercially. "RePave" is available for residential use in home centers and hardware stores. There are at least two New England firms in Massachusetts and Maine that produce "cold patch" mixtures with recycled asphalt shingles. The preliminary performance of recycled asphalt shingles in "cold patch" applications appears promising.(26) Vermont however had mixed results using roofing shingles in "cold patch" applications. The recycled asphalt shingles cold patch was determined to be 6% liquid binder, 14% ground asphalt and 80% aggregate. Some found the material to work very well and have long stick power and easy to use. Others found it too stiff to work with and low quality and therefore discontinued use of the product. Various mix design parameters are believed to be the reason some of the failures in Vermont 's experience with recycled asphalt shingles cold patch. It is believed however that using recycled asphalt shingles cold patch is a viable option in Vermont with further mix design modifications.(13)
Laboratory studies indicate that prompt roofing shingle scrap can also be used in stone-mastic asphalt applications, with the fiber contained in the shingle material effectively acting as an anti-draindown additive, preventing the asphalt cement from running off this relatively rich, coarse-textured asphalt mixture.(20)
Roofing Shingles as Aggregate
The Iowa Department of Transportation conducted a study where shingles ground down to pieces less than 1" were mixed with shingles ground down to less than 2". The mixture was spread to 2.5" thick over a limestone bed. After two years of observations, the shingles proved to be very effective at controlling dust on the rural road, allowed for better lateral control of vehicles, is a very cost effective method of recycling shingles and created a quieter roadway.(19) The Minnesota Department of Transportation also noted that using shingles as a dust suppressor is effective and does not require frequent re-application as other dust control media do.(26) The Greater Lebanon Refuse Authority in Pennsylvania has patented a process to use ground reproofing scrap as an alternative to gravel for roadways by mixing the scrap with crushed stone and spreading it between two layers of stone. This mixture has the ability to absorb oil that drips from automobiles and its porosity allows water to run through it. This road base has been used satisfactorily on Lebanon County landfill roads for two years.(26)
Vermont has also had success in using roofing shingles as aggregate. In Vermont shingles were double ground to less than 3/8" and mixed with recycled asphalt pavement (RAP) and gravel. The final mixture resulted in 60% gravel, 30% RAP and 10% recycled asphalt shingles. The mixture was placed on municipal roads and then evaluated for performance. Vermont found all trial applications to be successful. The mixture was easy to apply, compacted well, resisted rutting, erosion and mitigated dust. The persistence of nails in the mixture however would have to be addressed before the material could be marketed.(13)
MATERIAL PROCESSING REQUIREMENTS
Quality ControlNo special quality control techniques are required for prompt roofing shingle scrap; however, tear-off shingle scrap needs to be processed due to the presence of debris such as nails, wood, insulation, etc. Any debris must be removed to prevent equipment damage during size reduction and for beneficial use. The debris that contaminates tear-off roofing shingle scrap can be effectively removed. Nails are removed with magnets, paper and other lightweight contaminants are removed with blowers or vacuums. Asbestos testing can also be required for tear-off shingle by regulators.
Shredding
Roofing shingle scrap used in asphalt paving mixes is typically shredded into pieces approximately 13 mm (1/2 in) in size and smaller using a shingle shredding machine that consists of a rotary shredder and/or a high-speed hammermill.
Screening
Shredded shingles are typically discharged from the shredder or hammermill and screened to the desired gradation and stockpiled. Experience indicates that the size of the processed pieces should be no larger than approximately 13 mm (1/2 in) to ensure complete digestion of the roofing shingle scrap and uniform incorporation into the hot mix asphalt.(12) Scrap shingle greater than 13 mm (1/2 in) in size does not readily disperse, functioning much like aggregate. Particles sized too small can release the fibers, which act as a filler substitute(14) Shingles are often passed through processing equipment twice for effective size reduction.(26)
Watering
Water may be added during shredding to keep the shingles cool and control dust, but the added moisture is undesirable if they are to be used in HMA. As an alternative the shreds may be blended with other materials.(26)
Blending
As an alternative to watering shingles may be blended with up to 20% sand or screenings that would otherwise be added later in the production of HMA or cold mix asphalt patching material.(26) Processed roofing shingle material can resolidify during stockpiling, necessitating reprocessing and rescreening prior to introduction to the hot mix plant. To mitigate this problem, processed roofing shingle scrap may be blended with a carrier material such as sand or recycled asphalt to prevent the particles from sticking together.(13)
ENGINEERING PROPERTIES
Some of the properties of roofing shingle tabs that are of particular interest when roofing shingles are used in asphalt paving include asphalt content, asphalt hardness (penetration/viscosity), and aggregate gradation.Asphalt Cement (AC) Content: The asphalt cement contained in prompt roofing shingle scrap is typically between 25 to 35 percent by weight. Accurate determination of the prompt shingle scrap asphalt content and penetration is not possible using conventional Abson recovery techniques.(23) The release of shingle asphalt binder into the virgin binder can result in reduced virgin asphalt binder requirements. The point of introduction must minimize damage to the recycled asphalt shingles from excess heat and maximize softening of shingle asphalt binder to facilitate the blending of the shingle asphalt binder with virgin asphalt binder.(2) Extended soaking periods are required to extract and determine the available asphalt.
Asphalt Hardness (Viscosity/ Penetration): The precise determination of the AC viscosity and penetration is not possible because the roofing shingle asphalt is much harder than that normally used in asphalt concrete paving mixtures and contains fibers (which tend to stiffen asphalt concrete mixtures). The recycled asphalt shingle asphalt binder will mix with the virgin asphalt binder to create a final blended binder. The properties of the shingle asphalt binder may be considerably different from virgin asphalt binder. If the quantity of recycled asphalt shingle asphalt binder exceeds .75% by weight of the new HMA, the properties of the final blended binder may be measurably different from the design performance grade set forth by the local jurisdiction. The designer must be prepared to adjust the performance grade of the virgin binder to compensate for this difference. Roofing shingle scrap must be blended with a much softer (higher penetration/lower viscosity) asphalt cement binder for use in hot mix asphalt.
Gradation: Roofing shingle aggregates (granules) consist of minus 4.75 mm (No.4 sieve size) particles, which supplement the fine aggregate fraction of hot mix asphalt . Shingle aggregate from recycled asphalt shingles will affect the gradation properties of the new HMA. The designer must determine the particle size and fraction of shingle aggregate present and adjust the virgin aggregate composition to meet the required gradation properties.
Some of the mix properties that are of interest when roofing shingles are incorporated into asphalt pavements include the stiffening influence of roofing shingle fibers, strength, and stripping.
Stiffening Influence of Roof Shingle Scrap: Due largely to the influence of shingle fibers, laboratory studies indicate that incorporating prompt roofing shingle scrap in asphalt mixes tends to improve the high temperature susceptibility and rut-resistant properties of the mix.(1,7,14) Test results also indicate improved fatigue life of pavements with increasing roofing shingle scrap content.(1) Mixtures containing greater than 5% shingles may have a substantial decrease in mixture stiffness without a corresponding positive influence on cold temperature susceptibility. This may result in unacceptable stress at higher temperatures and high traffic volumes.(26)
Strength Characteristics: The use of prompt roofing shingle scrap (ranging from 3 to 5 percent by mass of the total mix) results in a denser pavement under compactive effort. While cold tensile strengths are reduced by the addition of roofing shingle scrap,(20) resilient modulus testing indicates that potential for low-temperature cracking is not substantially affected.(1,10,20)
The strain capacity of mixes with scrap shingles appears to be related to shingle type. Mixes containing organic felt shingle scrap exhibit slightly higher strain capacity than those with glass felt shingle scrap.(20)
Stripping: The moisture sensitivity of asphalt mixtures (an indication of stripping potential) does not appear to be significantly affected by the addition of prompt roofing shingle scrap,(14,20) but could be adversely affected by old, used roofing shingle scrap.(20)
DESIGN CONSIDERATIONS
Mix DesignThe specifications for new roofing shingles are set out in ASTM D255(6) and ASTM D3462,(9) which provide information on the material constituents. Currently the Standard Specification for Use of Reclaimed Asphalt Shingle as an Additive in Hot Mix Asphalt has been submitted for publication. The scope of the specification includes the incorporation of recycled asphalt in HMA. It does not cover the use of recycled asphalt shingles in hot-in-place pavements, cold in-place pavements or cold recycled pavements.(5) A Standard Recommended Practice for Design Considerations when using Reclaimed Asphalt Shingles in Hot Mix Asphalt has also been submitted for publication. This document includes the following sections to aid the mix designer in the design of HMA with RAS: 1. Design Considerations When Using Reclaimed Asphalt Shingle in New Hot Mix Asphalt, 2. Determining the Shingle Aggregate Gradation, 3. Estimating the Contribution of the Shingle Asphalt Binder to the Final Blended Binder in New Hot Mix Asphalt, and 4. Determining the Virgin Performance Grade and Percentage of the Virgin Asphalt Binder in the New Hot Mix Asphalt.(2)
Roofing shingle scrap (both organic felt and/or fiberglass felt) incorporated into asphalt paving mixes modifies the binder and also acts as a fine aggregate and mineral filler. Typically, an increase in filler content lowers the optimum asphalt cement content and increases the density and stability of the mix. Higher filler content can adversely affect durability due to reduction of voids in the mineral aggregate and optimum asphalt cement content. Also, excessive mineral filler can increase the surface area of the aggregate, reducing the asphalt film thickness.
Roof shingle scrap may be susceptible to moisture-related damage (stripping) and, therefore, the mix design should include a stripping resistance or retained stability test such as AASHTO T283(3) or MTO LS-283.(23)
Structural Design
Conventional AASHTO pavement design methods are appropriate for asphalt pavements incorporating roof shingle scrap in the mix.
CONSTRUCTION CONSIDERATIONS
Material Handling and StorageAccommodation must be made to avoid agglomeration of processed roofing shingle scrap, which can result in poor dispersion in the paving mix. One method of controlling agglomeration is to shred the material at the asphalt plant, immediately prior to introduction into the mixer. Shingles have been mixed with recycled asphalt pavement to prevent clumping in the stockpile.(26)
Mixing, Placing and Compacting
Processed roofing shingle scrap can be blended with fine aggregates in a pugmill (at a ratio of three parts roofing shingle scrap to one part fine aggregate).(12) The fine aggregate acts as a carrier for the shingle scrap, preventing agglomeration and producing a material that can be stockpiled, handled, and fed through the existing recycle system of a batch or drum mix plant.
The same methods and equipment used for conventional pavements are applicable to asphalt pavements containing roofing shingle scrap.
Quality Control
The same field testing procedures used for conventional hot mix asphalt mixes should be used for mixes containing roofing shingle scrap. Mixes should be sampled in accordance with AASHTO T168,(4) and tested for specific gravity in accordance with ASTM D2726 (7) and in-place density in accordance with ASTM D2950.(8)
ENVIRONMENTAL CONSIDERATIONS
Asbestos content in tear-off roofing shingles continue to be a concern for regulators.(16) A rigorous literature review and compilation of asbestos testing data was compiled in 2007 and found that asbestos was detected in just over 1% of the samples (out of 27,000).(28) Asphalt shingles contain asphalt a peteroleum derived product that contains polycyclic aromatic hydrocarbons (PAHs). Questions have been raised as to whether ground up shingles pose a direct or leaching exposure risk, as well as potentially impacting hot mix asphalt plant emissions.(28) There is no literature to indicate emissions at hot mix plants are any different using shingles. Further research on the leachability is currently being conducted in Florida.REFERENCES
- Ali, N., J. S. S. Chan, A. Potyondy, R. Bushman, and A. Bergan, "Mechanistics Evaluation of Asphalt Concrete Mixtures Containing Reclaimed Roofing Materials," Presented at the Transportation Research Board 74th Annual Meeting, Washington, D.C., January, 1995.
- American Association of State Highway and Transportation Officials. " Provisional Standard Recommended Practice for Design Considerations when using Reclaimed Asphalt Shingles in New Hot Mix Asphalt (R2005A-TS-2c) " Final publication in preparation.
- American Association of State Highway and Transportation Officials. Standard Method of Test, "Resistance of Compacted Bituminous Mixtures to Moisture Induced Damage," AASHTO Designation: T283-85, Part II Testing, 14th Edition, 1986.
- American Association of State Highway and Transportation Officials. Standard Method of Test, "Sampling Bituminous Paving Mixtures," AASHTO Designation: T168-82, Part II Tests, 14th Edition, 1986.
- American Association of State Highway and Transportation Officials. " Use of Reclaimed Asphalt Shingle as an Additive in Hot Mix Asphalt: A Provisional Standard Specification (M2005A-TS-2c) " Final publication in preparation.
- American Society for Testing and Materials. "Asphalt Shingles (Organic Felt) Surfaced with Mineral Granules", ASTM D255, Annual Book of ASTM Standards, Volume 04.04, American Society for Testing and Materials, West Conshohocken , PA, 1996.
- American Society for Testing and Materials, Standard Specification D2726-96, "Bulk Specific Gravity and Density of Non-Absorptive Compacted Bituminous Mixtures," Annual Book of ASTM Standards, Volume 04.03, ASTM, West Conshohocken , Pennsylvania , 1996.
- American Society for Testing and Materials. Standard Specification D2950-96, "Density of Bituminous Concrete in Place by Nuclear Methods,"Annual Book of ASTM Standards , Volume 04.03, ASTM, West Conshohocken , Pennsylvania , 1996.
- American Society for Testing and Materials. "Asphalt Shingles Made From Glass Felt and Surfaced with Mineral Granules", ASTM D3462,Annual Book of ASTM Standards, Vol. 04.04, ASTM, West Conshohocken , PA , 1996.
- Baker, R.F. and E. Connolly. "Ground Bituminous Shingle Mix," Presented at the January 1995 Transportation Research Board Annual Meeting, Washington , D.C.
- Foo, K.Y., Hanson, D. I., and Lynn, T. A., " Evaluation of Roofing Shingles in Hot Mix Asphalt ," Journal of Materials in Civil Engineering, Vol. 11, No. 1, February 1999, pp 15-20.
- "From Rooftops to Roads," Asphalt Contractor , July 1995, pp. 42-47.
- Grodinsky, C., Plunkett, N., Surwilo, J., "Perforrmance of Recycled Asphalt Shingles for Road Applications ", Final Report, Vermont Agency of Natural Resources, Chittenden Solid Waste District, September 2002.
- Grzybowski, K.F. "Recycled Asphalt Roofing Materials - A Multi-Functional, Low Cost Hot Mix Asphalt Pavement Additive," Use of Waste Materials in Hot Mix Asphalt, ASTM Special Technical Publication 1193, American Society for Testing and Materials, West Conshohocken, Pennsylvania, 1993.
- Janisch , D. and Turgeon, C., " Minnesota's Experience Using Shingle Scrap in Bituminous Pavements " Report No. MN/PR-96/34 , Minnesota Department of Transportation, 1996. NTIS.
- Johnson , J., " Group Tackles Asbestos Concern ". Waste News , January 22, 2007
- Justus, H. G. " New Jersey Department of Transportation Experience with Recycled Materials," Recovery and Effective Reuse of Discarded Materials and By-Products for Construction of Highway Facilities, FHWA Symposium, Denver , Colorado , October, 1993.
- Klemens, T.L. "Processing Waste Roofing for Asphalt Cold-Patches," Highway and Heavy Construction, April, 1991.
- Marks , Vernon J., and Petermeier, Gerald, "Let Me Shingle Your Roadway." Research Project HR-2079 , Iowa Department of Transportation, Ames , Iowa , 1997.
- Newcomb, D.E., M. Stroup-Gardiner, B. Weikle, and A. Drescher. Influence of Roofing Shingles on Asphalt Concrete Mixture Properties.Report prepared for Minnesota Department of Transportation at the University of Minnesota , March 1993
- Ontario Ministry of Transportation. "Resistance to Stripping of Asphaltic Cement in Bituminous Mixture by Immersion Marshall - LS 283," Laboratory Testing Manual, Ontario Ministry of Transportation, 1995.
- ORTECH, Leachate Test Reports, 1991, 1992 ORTECH International, Mississauga , Ontario , (Provided to JEGEL by IKO Industries Ltd., Brampton, Ontario, 1995.)
- Paulsen, G., M. Stroup-Gardiner, and J. Epps. Roofing Waste in Asphalt Paving Mixtures, Report 709-1, Center for Construction Materials Research, University of Nevada, Reno, Nevada, 1986.
- Turgeon, C.M. Waste Tire and Shingle Scrap Bituminous Paving Test Sections on the Munger Recreational Trail Gateway Segment, Report MN/RD-91/06; 9PR6002, Minnesota Department of Transportation, Office of Materials and Research, Maplewood, Minnesota, 1991.
- National Asphalt Pavement Association ( NAPA ) "Special Report 179, Uses of Waste Asphalt Shingles in HMA . January 1997.
- Vermont Agency of Natural Resources, " Recycled Shingles in Road Applications , " September 1999.
- Watson, Donald E., et al., " Georgia's Experience with Recycled Roofing Shingles in Asphaltic Concrete. " TRR 1638, Transportation Research Board. National Research Council, Washington DC 1998.
- Townsend, Tim; Powell, Jon; Xu, Chad "Environmental Issues", prepared for Construction Materials Recycling Association Asphalt Shingle Recycling Project, US EPA Innovations Workgroup, Innovative Waste Consulting Services, LLC, October 19, 2007.